It is almost a miracle to smoothly handle processes from idea to concept creation, from design development to functional prototyping, and from marketing operations to mass production. The development of products that are supported by international quality control mechanisms and care about customer satisfaction requires long-term analysis, meticulously prepared planning, and qualified teams. Each group plays an important role in the process of identifying, designing, building, testing and delivering the product.
The challenges of creating a new product increase the need for new rapid manufacturing technologies and manufacturing companies with high levels of integration capabilities each passing day. Today, new product development services seem to destruct many traditional manufacturing methods in the world.
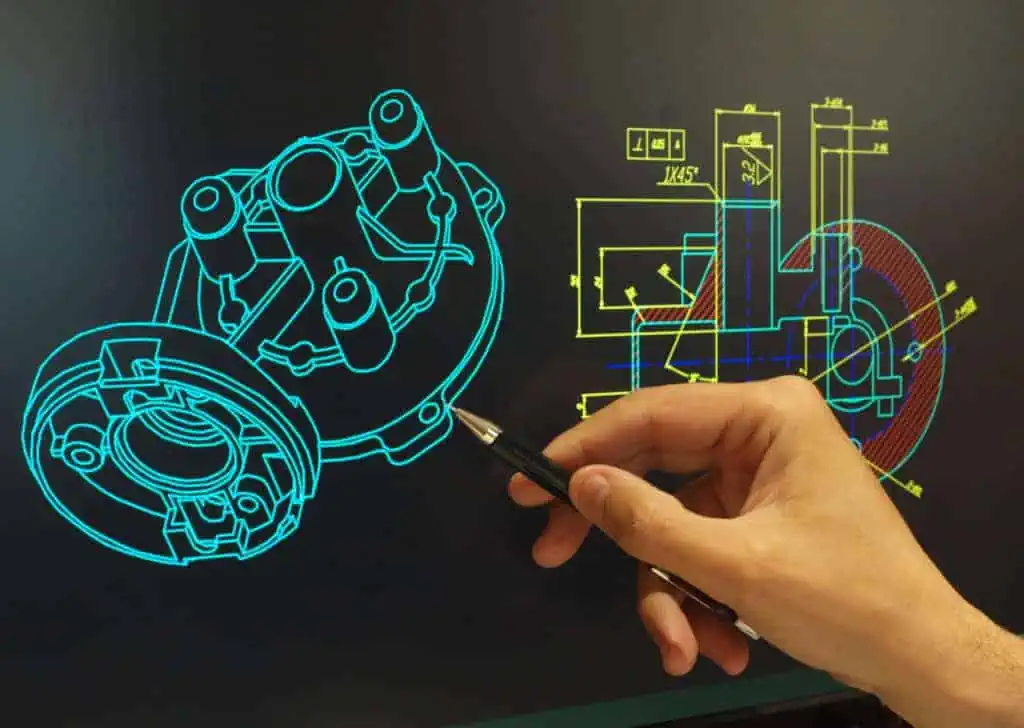
Process Planning and Manufacturing Analysis
Tests, cost and time plans, and manufacturability analyses are conducted to prove that your idea is feasible before starting product development. These studies will prevent you from making the wrong decisions. Developing new terms, equipment, and concepts is another critical step for feasible ideas. Experiencing unpredictable challenges while creating objective evidence is part of the pre-manufacturing analysis process. Despite all these meticulous studies, it is always possible to make gross errors or fine-tuning errors in the product development process. Therefore, it is very essential to have a pre-investment to solve the problems that may arise. Working with a manufacturer or a number of manufacturers with process stability and sufficient manufacturing capabilities plays an important role in ensuring that you minimize setbacks and the amount of pre-manufacturing capital.
Today, many companies, project teams, and engineers are aware of the fact that processes such as detailed verification, research, planning, concept, and concept development are important in terms of ensuring product development projects without any problems. Arranging many steps, which you will take to survive in the competitive market conditions, meet consumer demand, and increase the market share of the product, in the analysis process determines the lifecycle and success of your product.
Prototyping
Experiencing what a product you want to manufacture really looks like allows you to notice several mistakes in advance. Subjecting a product whose design has been completed and that is free from aesthetic constraints to some mechanical and chemical performance tests to meet the desired standards is an integral part of the prototyping and testing process. In the product development process, you can achieve the perfect design only through this trial and error process.
Today, with the development of 3D printing and CNC machining technologies, it has become possible to develop a comprehensive prototype in a very short time. Producing prototypes close to the final product design is considered a reasonable strategy to reduce pre-mas production and mass production costs depending on the product properties desired, manufacturing time, and quality requirements.
Instead of creating multiple prototypes to test mechanical suitability, chemical resistance, or design manufacturability, you can quickly resolve errors arising from tolerance and design constraints by creating comprehensive prototypes that can show end-product performance.
Determining Market Needs
Correctly identifying market and customer needs analysis is the most critical step before proceeding to pre-mass production. Defects detected in this step, where you can test the need for your product, and the feedback you receive will save you time and money, as well as contribute to the perfection of your product.
Low-Volume Manufacturing (Pre-Mass Production)
In this stage, your design becomes a physical product ready for mass production. The data you will collect throughout the process is the last opportunity to apply the essential changes before sending the product to mass production.
In this process, you will interact with potential users by determining the volume of the low-volume manufacturing according to demand, and it constitutes all of the applications where product demand will be tested. After analyzing the test results and implementing the improvements, you can share the test results to reveal the potential success of your product. This success depends on the selection of the target audience, the accuracy of customer needs analysis, and the fulfillment of quality and design requirements in prototyping.
The products you need for pre-mass production are manufactured by injection molding, silicone molding, CNC machining, or Industrial 3D printing methods depending on the quality standards, certificates, or volume. Depending on the requirements of your product, you may need multiple manufacturing technologies. Your physical product makes the most real communication with the market at this stage.
Mass Production
Until the mass production stage, you must be confident of the iteration steps you take in pre-mass production and be ready to test your final product. At the same time, your development team must complete all the work related to your website and software requirements and make your product ready for going live at this stage. If all these issues are finished, it is time to switch to mass production and measure the live experience with success metrics.
Machines and technologies designed for the manufacturing industry have been developed to achieve the optimum manufacturing performance and cost for certain products. 5-axis CNC machining centers or industrial 3D printers are designed to meet all kinds of manufacturing needs. With these features, CNC machining or 3D printing techniques are usually ideal manufacturing technologies for low- and medium-volume manufacturing needs. However, if mass manufacturing is required for a single product, customized injection molding technology is the most appropriate method.
Scaling your work is very important when determining or increasing your manufacturing volume. This means that you can reduce costs while manufacturing more products. Factors such as purchasing a high volume of raw materials, manufacturing planning, successful advertising strategies, high-level supply chain experience, productive employees, and accurate determination of the manufacturing volume are key to the success of your manufacturing and the yield of your company.
Collaborating with Right Manufacturers & Suppliers
Let us assume that you are ready to launch a new product. You need qualified partners and professional teams to support you in the manufacturing, marketing, storage, distribution, return of products, etc. You can determine the lifelong quality cycle of your product by collaborating with teams specialized in manufacturing technologies, concept development, quality control, and procurement for manufacturing your products that can be adopted by the market.
Multiple manufacturing sites, design, material, and manufacturing engineers, quality control and marketing specialists, and sales staff will be directly related to the success of your product in its journey from the idea stage to the mass production stage before putting it on the market. The manufacturer that will meet your requirements in prototyping and the manufacturer that will provide the most appropriate service for mass production will probably be different. You can use manufacturing technologies such as industrial 3D printing or CNC machining for mold manufacturing, prototyping, or part manufacturing. All these searches that allow you to create your supply chain step by step will result in a serious loss of time and money. Errors due to communication problems are another aspect of the industrial manufacturing process.
Thanks to end-to-end digital process management with sustainable high-quality, quick delivery, and affordable price optimization, Xometry has the largest manufacturing network in Turkey. With its online platform where you can access all manufacturing technologies from a single point, Xometry always supports you in your product development processes. In addition to the opportunity to work with hundreds of suppliers that are specialized in their fields and who will be determined according to your production needs, our engineers, who are specialized in their fields, are just a phone call away to support your product development processes. Thanks to our smart platform supported by artificial intelligence, you can upload your designs at the idea stage to our system for free. With manufacturability analysis and guaranteed high-quality control mechanisms, we can proceed your prototypes to the mass production stage by spending much less time and money.
Comment(0)