Klokkengroep ‘s-Hertogenbosch is a group of over 100 clockmaking enthusiasts, ranging from retired manufacturing experts to complete beginners. Together, we share a passion for building and restoring timepieces, often designing and crafting them from scratch in our workshops.
In June 2024, we embarked on our most ambitious project to date: recreating the Barentsz Clock, a mediaeval timepiece with an extraordinary history. To bring this piece of history to life, we combined traditional horological techniques with cutting-edge manufacturing methods, including precision waterjet cutting sourced from Xometry.
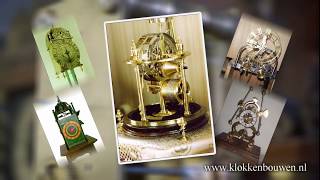
Passing on Craftsmanship: A Year of Traditional Training
Our society is dedicated to preserving traditional machining and horological skills through a year-long program. Weekly sessions combine theory with hands-on practice, where trainees build a simple weight-driven clock from raw materials like brass sheets and steel rods. This project introduces essential techniques such as gear cutting, precision boring, and assembly.
The workshop is equipped with high-precision tools, including Swiss Schaublin 102 VM lathes, Aciera F3 milling machines, and Austrian EMCO lathes, enabling members to master both traditional and modern machining methods.
During the training program, members create a weight-driven clock entirely from scratch, using brass sheets for the wheels and steel rods for the shafts and pinions. This straightforward design introduces essential techniques like gear cutting, precision boring, and assembly, forming a strong foundation for tackling advanced projects like the Barentsz Clock.
The Inspiration Behind the Barentsz Clock Project
The Barentsz Clock dates back to the late 1500s and accompanied Willem Barentsz on his Arctic expedition. The clock was one of many elaborate gifts meant for high-ranking officials in the Far East. However, the expedition failed when Barentsz’s ship, “De Witte Swaen” (The White Swan), became trapped in the ice near Nova Zembla.
The crew endured a harsh Arctic winter in a wooden shelter, Het Behouden Huijs (The Safe House), constructed from the ship’s remains. The clock was left behind when they escaped, and it wasn’t until 1871 that a Norse hunter rediscovered it alongside the remains of the shelter. Now part of the Rijksmuseum collection in Amsterdam, the clock is a rare surviving example of mediaeval horology.
Recreating this historical masterpiece was not a solo endeavour; it became a collaborative effort involving multiple members of the Horological Society. Each participant contributed their unique skills and expertise, from researching historical methods to adapting modern manufacturing techniques. This collective passion and teamwork were essential to bringing the Barentsz Clock back to life.
Revealing the Secrets of the Barentsz Clock
The Barentsz Clock stands out as an exceptional example of mediaeval horology. Unlike many other historical clocks, it has never been modernised, preserving its original design. Every component was crafted entirely from steel, using intricate hot-forging techniques that showcased the exceptional skill of mediaeval smiths.
Creating a single geared wheel involved a multi-step process:
- Forging a bar with a rectangular profile.
- Bending the bar into a round hoop.
- Hot-welding the hoop to form a closed ring.
- Marking 64 punch points for the teeth.
- Hammering the tooth profiles into the red-hot hoop.
- Creating a steel cross for the spokes.
- Hot-welding the spoke cross to the wheel ring.
- Filing the teeth to their final profiles.
Such methods, while remarkable for their time, are beyond the reach of traditional manufacturing today. No current traditional manufacturing technology can hope to match these mediaeval smithing skills. As these methods are far beyond reach today, some replica builders opt for easier-to-make brass wheels, which became popular in the mid-17th century.
The Process: Blending Old Techniques with Modern Manufacturing
To recreate the 48 steel gearwheels needed for the 8 copies of the Barentsz Clock, our society turned to waterjet cutting—a modern manufacturing technique that perfectly aligns with the intricate craftsmanship of the original design. This approach allowed us to replicate the sharp corners and thin spokes of the steel wheels with exceptional precision while maintaining the material’s integrity.
By using waterjet cutting, we avoided the need for additional finishing on the cut edges, leaving the wheels ready for gear cutting and precision boring in our workshop. This seamless integration of modern technology ensured the steel wheels retained the intricate design and authenticity of their mediaeval counterparts, paying homage to the original artisans’ expertise while embracing 21st-century efficiency.
The resulting replicas are fascinating not only from a horological and manufacturing perspective but also visually. These clocks give an approximation of time rather than precision, with a daily accuracy of give or take an hour. As a result, the clocks feature only one hand.
Exploring New Horizons: The Role of 3D Printing
The Horological Society continuously balances its respect for traditional craftsmanship with an openness to modern innovation. One such innovation is the use of 3D printing, which has become an invaluable tool for prototyping clock components in plastic. By sourcing high-quality 3D-printed parts through Xometry, we should be able to test designs efficiently before committing to metal production. This approach allows us to refine intricate mechanisms like gear assemblies with minimal waste and cost.
Looking to the future, we see great potential in metal 3D printing for creating highly intricate parts such as Tourbillon cages. These components, often regarded as the pinnacle of horological craftsmanship, could open new possibilities for blending precision engineering with creative design in our clockmaking projects. With Xometry’s advanced manufacturing services, we are well-positioned to explore these possibilities and continue innovating in the field of horology.
For those interested in learning more about the Barentsz Clock, Cees Wijnberg’s book, “Het uurwerk van de Barentsz-expeditie 1596”, offers detailed insights into its history and guidance on building a replica. The book is available through the Museum Zaanse Tijd.
Learn more about the Barentsz Clock and Cees Wijnberg’s work here.
Share Your Engineering or Product Design Story
Share Your Story!
Share your engineering and product design journey and get a €300 reward! Showcase your innovative solutions and best practices with our community.
Comment(3)