During a previous research project, a team at the Technical University of Augsburg (Germany) and I developed a legally binding test procedure for sewage pressure pipes in operation. While conducting on-site pressure tests in the sewer networks of various operators, we discovered a significant issue: nearly 50% of the pressure pipes were not in a sealable condition at their ends. Given that pressure pipes account for approximately 10% of the entire sewer system, this posed a major problem—if a pipe cannot be properly sealed, entire sewer shafts might have to be replaced, an extremely costly and time-consuming process.
This discovery motivated me to develop a universal joint that could quickly and cost-effectively seal pressure pipes, preventing unnecessary infrastructure replacements.
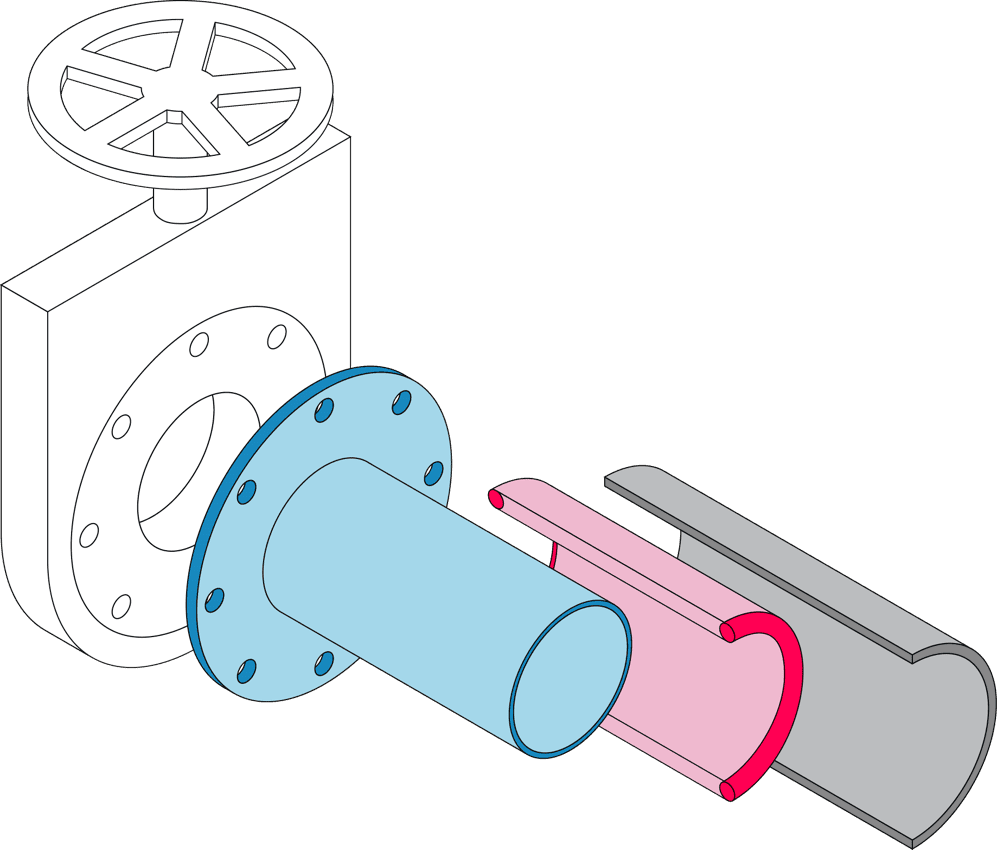
Developing a Universal Solution
For ease of use, the universal joint should serve as a versatile, one-size-fits-all solution, seamlessly adapting to pipes of different sizes and materials – which is also the biggest challenge in this development. Additionally, sewer environments are extremely harsh—constant sewage flow, chemical exposure, and high mechanical loads mean that any solution must be both durable and easy to install. Since wastewater is always flowing, the installation process needed to be quick and reliable, with minimal disruption.
Our development process began with extensive brainstorming on potential shapes and sealing methods. 3D printing played a crucial role in this phase, allowing us to rapidly test different designs before committing to final production materials. Since the final materials were too costly and time-intensive for early prototyping, we focused on creating small-scale test models in-house, while Xometry produced the larger prototypes for convenience and accuracy.
Refining the Design and Selecting the Right Materials
In cooperation with the Technical University of Augsburg, we started with a student project group to research the best materials and adhesives for the universal joint. Adhesion was a particularly challenging aspect as all common materials from cast iron, fiber cement to PVC and PE (Polyethylene) needed to be suitable for adhesion. Plastics, in particular, are difficult to bond because of their smooth surface. The durability of the connection as well as the even distribution of the adhesives are crucial for long-term performance. Since we needed to test this in real-world conditions, we printed the models at a 1:1 scale to replicate actual installation scenarios.
Through multiple iterations, we refined the joint’s shape, sealing method, and installation process. The latest prototypes include spacers for precise alignment and have been successfully tested with transparent pipes to evaluate bonding and sealing effectiveness.
Scaling for the Future
While 3D printing has been invaluable for prototyping and testing, our next step is to transition to CNC machining or injection molding for the final production parts. These methods will allow us to achieve the necessary strength, durability, and scalability for widespread use in real sewer systems. We are in contact with several network operators who are interested in this development. Additionally, we are in contact with sewage pipeline construction companies that currently install traditional closures for wastewater pressure pipes. Our development must match or outperform these solutions in cost and installation efficiency.
Looking ahead, we are continuing to test and refine the design, with the goal of bringing the universal joint to market. This innovation has the potential to significantly reduce costs for sewer operators—and indirectly for you as well, since the sewer network is funded through fees included in the water charge and, reduces unnecessary infrastructure replacements.
Lessons Learned and Advice for Innovators
One of the biggest lessons from this project has been the importance of iteration and flexibility. No solution is perfect from the start—each prototype, failure, and adjustment brings us closer to an optimized product. My advice to others tackling similar engineering challenges is to embrace rapid prototyping, leverage expert collaborations, and stay open to unexpected insights that can improve your design.
At BK Pipecheck, we are committed to making wastewater infrastructure more efficient, reliable, and cost-effective, and I look forward to seeing how this universal joint can make a real impact in the industry.
Learn more about BK Pipecheck: https://bk-pipecheck.de/ and Johannes Königs project.
Have you developed a smart solution for aging infrastructure or challenging environments? Share your experiences, ideas, or questions about designing innovative, cost-effective fixes for real-world engineering problems!
Share Your Engineering or Product Design Story
Share Your Story!
Share your engineering and product design journey and get a €300 reward! Showcase your innovative solutions and best practices with our community.
Comment(0)