Plastic injection molded parts often require finishing for the end use. There are a variety of surface finish options available for injection molding that influence the texture, look, feel, and other surface characteristics of the parts. Not only from a customer point of view but also from a designer’s and engineer’s perspective, it’s an important design consideration as it is essential for the mold design.
Need for Surface Finishing
Most molds are machined from aluminium and/or steel and the molded part will pick up even the smallest imperfection in the mold surfaces. The machining marks left by the end mills will be transferred to the molded part if not removed by bead blasting or polishing. In many cases, particularly on the inside of a part which is not visible to the eye, the tooling marks can be left on the mold and it will make no difference to the function or cosmetics of the part.
Those surfaces which are visible, however, require additional finishing. Almost all molds are finished to some degree, but the more polishing required, the higher the cost of the mold tooling and the longer it will take to complete the mold.
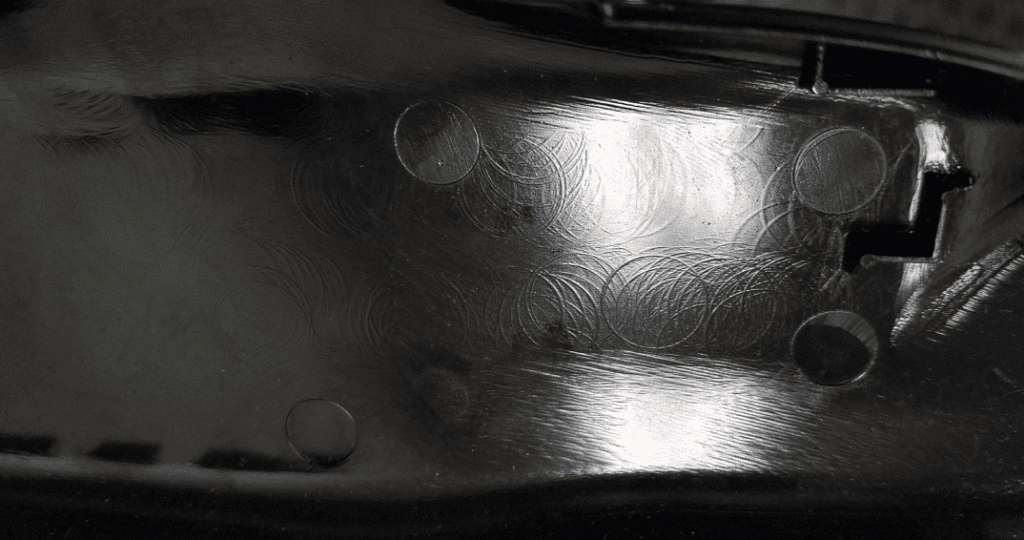
Prime Factors Deciding the Surface Finish
Surface finishing in injection molding is different from CNC machining or 3D printing surface finishes. While in the latter two, surface finishing is done after the part is made, as an extra step, whereas in the former, the mold surface itself is prepared in such a way (texturing) that the part comes out finished. For example, if the required part needs a matte finish, the inside of the mold is textured in such a way that the molded part comes out with a matte finish. Here are the factors that decide the finish:
Increasing the Visual Appeal of the Part
Part designers may choose texturing for several aesthetic reasons. A smooth or matte texture on the surface of a part not only improves the appearance and gives a finished look but also hides the imperfections such as flow lines, knit lines, sink marks and shadow marks that are caused as a result of injection molding. From a commercial perspective, parts with good surface finish appeal to the customer.
Improving the Functionality of the Part
Surface texturing improves paint adhesion and sticker adhesion. For example, a matte textured part can easily hold the paint on it for a longer time and is even good for sticking a label. It also improves the gripping of the part. By texturing the mold surface, we can also avoid plastic defects like short shots and flash. A properly designed and textured mold can also help in escaping the trapped gasses.
SPI Surface Finish for Injection Molding
The Society of Plastics Industry (SPI) has set several standard finishing procedures that result in different part surface finishes. The mold can be textured with machines or polished manually. They are explained in the below table.
SPI finish | Description | Applications | Surface roughness (Ra µm) |
Suitable materials |
A-1 | Grade #3, 6000 Grit Diamond Buff | High polish parts | 0.012- 0.025 | Acrylic |
A-2 | Grade #6, 3000 Grit Diamond Buff | High polish parts | 0.025-0.05 | Acrylic, PC |
A-3 | Grade #15, 1200 Grit Diamond Buff | High low polish parts | 0.05-0.10 | ABS, Acrylic. PS, Nylon, PC |
B-1 | 600 Grit Paper | Medium polish parts | 0.05-0.10 | ABS, Acrylic, PP. PS, HDPE, Nylon, PC |
B-2 | 400 Grit Paper | Medium polish parts | 0.10- 0.15 | ABS, Acrylic, PP. PS, HDPE, Nylon, PC |
B-3 | 320 Grit Paper | Medium low polish parts | 0.28-0.32 | ABS, Acrylic, PP. PS, HDPE, Nylon |
C-1 | 600 Stone | Low polish parts | 0.35-0.40 | ABS, Acrylic, PP. PS, HDPE, Nylon, TPU |
C-2 |
400 Stone | Low polish parts | 0.45-0.55 | ABS, Acrylic, PP. PS, HDPE, Nylon, TPU |
C-3 |
320 Stone | Low polish parts | 0.63-0.70 | ABS, Acrylic, PP. PS, HDPE, Nylon, TPU |
D-1 |
Dry Blast Glass Bead | Satin finish | 0.80-1.00 | ABS, PP. PS, HDPE, Nylon, PC, TPU |
D-2 |
Dry Blast #240 Oxide | Dull finish | 1.00-2.80 | ABS, PP. PS, HDPE, Nylon, TPU |
D-3 |
Dry Blast #24 Oxide | Dull finish | 3.20-18 | ABS, PP. PS, HDPE, Nylon, TPU |
VDI (STD) Surface Finish for Injection Molding
VDI 3400 Surface Finish (commonly known as VDI surface finish) refers to the mold texture standard set by Verein Deutscher Ingenieure (VDI), the Society of German Engineers. The VDI 3400 surface finish is mainly processed by Electrical Discharge Machining (EDM) when mold machining. It could also be done by the traditional texturing method (like in SPI). Although the standards are set by the society of German Engineers it is commonly used among tool makers all over, including North America, Europe, and Asia.
VDI values are based on the surface roughness. From the image, we see different textures of the surface finish with varying values of surface roughness.
VDI Value | Description | Applications | Surface roughness (Ra µm) |
12 | 600 Stone | Low polish parts | 0.40 |
15 | 400 Stone | Low polish parts | 0.56 |
18 | Dry Blast Glass Bead | Satin finish | 0.80 |
21 | Dry Blast # 240 Oxide | Dull finish | 1.12 |
24 | Dry Blast # 240 Oxide | Dull finish | 1.60 |
27 | Dry Blast # 240 Oxide | Dull finish | 2.24 |
30 | Dry Blast # 24 Oxide | Dull finish | 3.15 |
33 | Dry Blast # 24 Oxide | Dull finish | 4.50 |
36 | Dry Blast # 24 Oxide | Dull finish | 6.30 |
39 | Dry Blast # 24 Oxide | Dull finish | 9.00 |
42 |
Dry Blast # 24 Oxide | Dull finish | 12.50 |
45 |
Dry Blast # 24 Oxide | Dull finish | 18.00 |
Conclusion
Out of the two categories of injection molding surface finishes, SPI grade A and B are considered the smoothest with very low surface roughness and are more expensive. Whereas, from a surface roughness point of view, VDI 12, the highest quality VDI, equals SPI C grade.
Xometry offers both SPI and VDI surface finishes for injection moulding parts. Our injection moulding experts at Xometry would be happy to help to further advise you on the possible options. Feel free to upload your design to our quoting engine and we will get you a quote within 48 hours.
Get Your Free Injection Moulding Finishes Card
This card is moulded in black ABS plastic and depicts twelve SPI finishes from polished to coarse as well as common VDI 3400 surface textures on the back. It is a great tool to keep nearby when working on new injection moulding projects.
Delivery only across Europe (For the US request form follow here). Only 1 card per client. Only for companies
Comment(1)