If you’ve ever debated whether to use CNC machining or 3D printing for a project, you’re not alone. Both are powerful methods for manufacturing plastic parts, but they serve different purposes depending on your needs. CNC machining is like a sculptor, meticulously cutting away material to reveal your part, while 3D printing builds parts layer by layer, much like stacking bricks to create a solid structure.
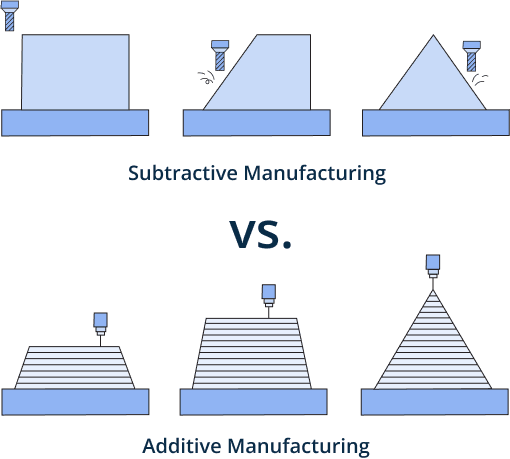
Each process has unique advantages—CNC machining delivers high precision and material versatility, while 3D printing shines for complex geometries and rapid prototyping. Determining which method to use depends on a variety of factors, from design complexity and material requirements to production speed and budget considerations.
Quick Reference Table
The following quick check table provides an at-a-glance comparison to help you assess which process might best suit your needs or if a combination of both could be utilized for optimal results.
Checklist: Choosing Between CNC Machining and 3D Printing for Polymers
Use this quick-reference checklist to evaluate which manufacturing process suits your project needs. For each question, find whether CNC machining, 3D printing (3DP), or both offer the best solution.
- Do you need uniform mechanical properties throughout the part? If yes, CNC machining is the best pick. It produces isotropic components with consistent mechanical and thermal properties throughout the material, ideal for load-bearing applications or mechanical assemblies. 3D printed parts have anisotropic characteristics due to their layered construction.
- Is high tensile strength critical for your part? Then CNC machining is the way to go. Components made with CNC machining often achieve 40–60% higher tensile strength than 3D-printed parts using the same materials, making it ideal for high-strength applications.
- Do you require a short production timeline? Choose 3D printing. Processes like SLS typically take 3–5 working days, including setup, printing, and post-processing. In contrast, CNC machining requires longer lead times—usually 10+ working days—due to extensive setup, programming, and tooling preparation.
- Are you producing a low volume of parts (1–10 units)? Then 3D printing is your best pick. It offers lower per-unit costs for small runs thanks to its minimal setup requirements.
- Are you producing high volumes (50+ units)? Opt for CNC machining. It becomes more cost-effective at high volumes as setup costs are distributed over a larger number of parts.
- Are flexible materials, photopolymers, or composite resins required? Your answer is 3D printing. It supports exclusive materials like TPU, TPE, specialized photopolymer resins, and composites not available in CNC machining.
- Is cost a primary concern?
- For low volumes (1–10 units), 3D printing is the more affordable option.
- For high volumes (50+ units), CNC machining becomes the cost-effective choice due to amortized setup costs.
- For medium volumes (10–50 units), consider MJF, which offers efficient build volume utilization at a reasonable cost.
- Do you need a manufacturing method that can scale for future production? Then CNC machining is the better pick. It’s well-suited for medium to high production volumes, where setup costs can be amortized across larger batches. On the other hand, 3D printing excels at one-offs and low-volume production but becomes less cost-effective as quantities increase.
Cost Drivers
Understanding the cost drivers for CNC machining and 3D printing can help you optimize your design and choose the most cost-effective process. From part geometry to required surface finishes, certain features significantly impact the production costs for each method.
Description | CNC Machining (€) | 3D Printing (€) |
Large, bulky geometries | ||
Coring and lightweighting features | ||
Off-angle holes | ||
Organic features | ||
Precision and tight tolerances | ||
Smooth surface finish | ||
Deep holes and channels |
Geometric Complexity Considerations
Manufacturing feasibility is heavily influenced by part geometry:
- Powder bed fusion processes (SLS, MJF) excel at producing complex freeform geometries without support structures.
- FDM and SLA require sacrificial supports for overhangs >45°.
- CNC machining is constrained by:
- Tool accessibility requirements.
- Minimum internal radius limitations based on cutting tool diameter.
- Inability to produce enclosed internal features.
- Limited undercut capabilities
If the part’s design includes features such as intricate internal structures, undercuts, or organic shapes that are not feasible with traditional subtractive manufacturing, additive technologies should be employed.
Material Properties and Process Compatibility Matrix
When designing parts that might involve both CNC machining and 3D printing, choosing the right engineering polymer is the first step. Ensuring material compatibility between the two processes is essential to achieving the desired performance and quality.
Some materials, like ABS, PA (Nylon), and PC, are versatile enough for both CNC machining and 3D printing. However, 3D printing also opens up options for specialized materials, such as flexible thermoplastics (TPU, TPE), photopolymer resins, advanced composites, and CLIP resins (Carbon DLS), which aren’t available for CNC machining.
When selecting the ideal material for your project, consider these key factors:
- Mechanical requirements: Does the part need to withstand high loads, impact, or wear?
- Environmental exposure: Will the part face extreme temperatures, chemicals, or UV exposure?
- Process compatibility: Is the material suitable for the chosen manufacturing method(s)?
- Budget: How does the material cost align with your project goals?
The table below highlights common materials, their properties, and the processes they work best with, helping you make an informed decision.
Material | Properties | CNC Machining Suitability | 3D Printing Suitability | Compatibility/Use Cases for Multi-Technique Parts |
ABS (Acrylonitrile Butadiene Styrene) | Good impact resistance, toughness, and moderate strength; easy to machine. | • Ideal for durable parts with complex shapes • Good dimensional stability |
• Popular for FDM 3D printing • Moderate detail and finish quality • Post-processing needed |
Great for enclosures or parts that need both machined precision and 3D-printed complexity. |
Nylon (Polyamide, PA) | High strength, toughness, and wear resistance; self-lubricating properties. | • Excellent for gears, bushings, and structural components • Easily machined |
• Suitable for SLS, MJF and FDM printing • Good flexibility and strength, moisture-sensitive |
Useful for gears, brackets, and structural parts, where both techniques can complement each other. |
Polycarbonate (PC) | High impact resistance, optical clarity, and heat resistance; prone to stress cracking. | • Works well for impact-resistant and heat-tolerant applications • Requires careful machining |
• 3D printing yields strong parts • FDM requires an enclosed chamber for heat control |
Suitable for protective covers, impact-resistant parts, or assemblies combining printed and machined pieces. |
POM (Polyoxymethylene, Acetal/Delrin) | High stiffness, low friction, and excellent dimensional stability; resistant to wear. | • Ideal for precision parts like gears, cams, and bearings • Smooth surface finish |
• Not commonly used in 3D printing but can be printed using special setups (e.g., POM filaments) | Best suited for assemblies that need tight tolerances in machined components and lightweight 3D-printed parts |
PEEK (Polyether Ether Ketone) | Exceptional mechanical strength, chemical resistance, and high-temperature tolerance. | • Preferred for aerospace, medical, and high-performance components • Costly but precise |
• Available in specialty 3D printers (FDM or SLS) • Very strong but limited design flexibility |
Ideal for highly demanding environments, combining precision machining and complex 3D-printed features. |
PETG (Polyethylene Terephthalate Glycol) | Good chemical resistance, strength, and ease of printing; more ductile than ABS. | • Suitable for clear parts and applications needing good mechanical properties | • Common for FDM printing • Offers a balance of strength, flexibility, and ease of use |
Well-suited for structural parts or enclosures that may need a mix of machined precision and flexible printing. |
Polypropylene (PP) | High fatigue resistance, chemical resistance, and flexibility; low density. | • Good for living hinges, chemical containers, and flexible parts • Tricky to machine |
• Hard to print but possible with proper bed adhesion techniques • Flexible and durable |
Useful for creating chemical-resistant parts or containers that may combine printed features with machined components. |
Mechanical Property Comparison: CNC Machining vs 3D Printing
Let’s compare the key differences in the mechanical properties of materials like ABS, PC, and PA12 when CNC machined or 3D printed.
ABS (Acrylonitrile Butadiene Styrene)
Property | CNC Machined | 3D Printed (FDM) |
Tensile Strength | 40-45 MPa | 30-35 MPa |
Impact Strength (Izod) | 200-220 J/m | 95-130 J/m |
Elastic Modulus | 2.3-2.4 GPa | 1.8-2.0 GPa |
Compression Strength | 46-48 MPa | 35-40 MPa |
Key factors affecting properties for 3D printing:
- FDM layer adhesion strength.
- Print orientation (Z-axis typically weakest).
- Environmental conditions during printing.
- Infill percentage (100% used for comparison).
PC (Polycarbonate)
Property | CNC Machined | 3D Printed (FDM) |
Tensile Strength | 65-70 MPa | 55-60 MPa |
Impact Strength (Izod) | 600-850 J/m | 250-400 J/m |
Elastic Modulus | 2.3-2.4 GPa | 2.0-2.1 GPa |
Compression Strength | 75-80 MPa | 60-65 MPa |
Key factors affecting properties for 3D printing:
- Higher printing temperature requirements.
- Moisture sensitivity during processing.
- Chamber temperature control.
- Cooling rate effects.
PA12 (Nylon 12)
Property | CNC Machined | 3D Printed (SLS/MJF) |
Tensile Strength | 70-85 MPa | 48-55 MPa |
Impact Strength (Izod) | 150-180 J/m | 110-130 J/m |
Elastic Modulus | 1.7-1.8 GPa | 1.4-1.5 GPa |
Compression Strength | 65-70 MPa | 50-55 MPa |
Key factors affecting properties for 3D printing:
- Powder recyclability effects.
- Sintering parameters.
- Part density achievements.
- Post-processing methods.
When to Choose Injection Molding Over CNC Machining or 3D Printing
While CNC machining and 3D printing each have their strengths, there are scenarios where neither method fully satisfies the requirements for cost-effectiveness, high-volume production, or exceptional uniformity. In such cases, injection molding (IM) becomes a powerful alternative. This process is particularly well-suited for large-scale production runs, intricate designs, and applications that demand high precision and consistency.
Here’s a breakdown of when injection molding is the better choice:
- You’re looking for cost efficiency in large-scale production: Injection molding excels in high-volume production because its upfront tooling costs are offset by extremely low per-part costs during large runs (e.g. mass production of consumer goodsl like plastic containers). While CNC machining and 3D printing can handle low- to medium-volume production, they become cost-prohibitive at this scale.
- You need consistent quality and flawless surface finishes: If your parts require strict dimensional tolerances or impeccable surface finishes, injection molding delivers unmatched uniformity across all units. This is particularly important in industries like medical devices, electronics, and precision engineering, where consistent quality is critical.
- Your design includes thin walls or complex features: CNC machining struggles with thin walls, while 3D printing can produce them but may lack precision. Injection molding, on the other hand, can easily replicate intricate features like thin walls, living hinges, and undercuts, thanks to its ability to use highly precise molds (e.g. packaging components with snap-fit features).
- You need a wide variety of materials with specific properties: Injection molding supports a vast array of materials, including advanced engineering polymers and custom formulations. This makes it ideal for projects that require specific chemical, thermal, or mechanical properties, such as high UV resistance or chemical durability.
Final Decision Guidelines for CNC Machining and 3D Printing of Polymers
Choose CNC Machining When
- Precision and durability are key: CNC machining excels in delivering high dimensional accuracy and robust parts, ideal for applications requiring long-term durability and precision, such as aerospace and medical components.
- High production volume is expected: For large batch production, CNC machining becomes more economical over time, as the setup costs are distributed across a larger number of parts.
- Premium surface finish is required: CNC machining can achieve excellent surface finishes with minimal post-processing, making it suitable for components where aesthetics or precise fitting are crucial.
Choose 3D Printing When
- Rapid prototyping and design flexibility are needed: 3D printing is ideal for quickly iterating on complex, custom designs, as the technology allows for intricate geometries and internal structures that are challenging or impossible to machine.
- Environmental impact and material efficiency matter: The additive nature of 3D printing minimizes material waste, making it an excellent choice when sustainability is a priority.
- Low Volumes and Budget Constraints Apply: For small production runs, 3D printing is typically more cost-effective due to lower setup costs and faster initial production, suitable for prototypes or limited custom parts.
In cases where both high precision and complex geometries are required, combining CNC machining for critical tolerance areas with 3D printing for intricate, lower-stress sections could be a powerful approach.
Comment(0)