Le thermoformage, un processus de fabrication de plastique, moule des feuilles thermoplastiques dans les formes souhaitées à l’aide de la chaleur. Historiquement, ses origines remontent aux anciennes pratiques de chauffage des matériaux pour les façonner, mais les innovations modernes ont affiné ses applications et élargi son utilité. Actuellement, le thermoformage est essentiel dans la fabrication contemporaine grâce à sa flexibilité, son efficacité et sa rentabilité.
Qu’est-ce que le thermoformage ?
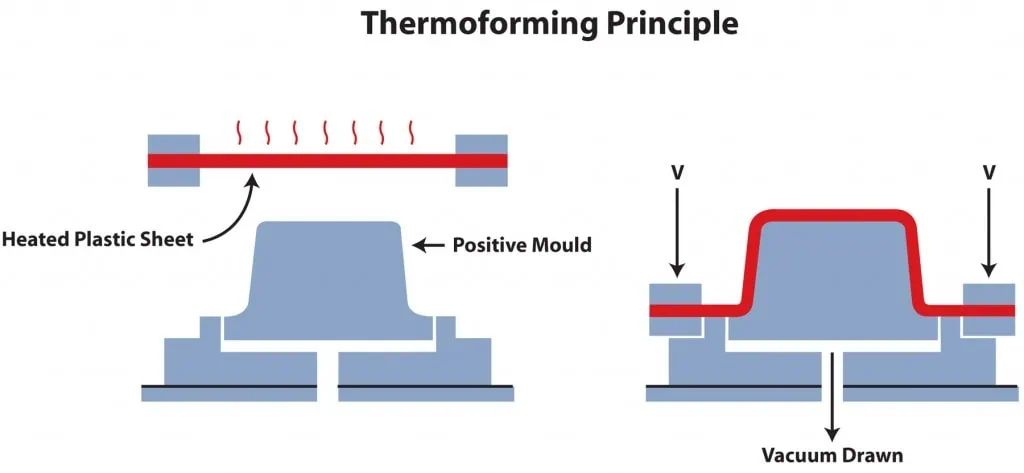
Le thermoformage est une technique de fabrication sophistiquée qui consiste à mouler des matériaux thermoplastiques en des formes tridimensionnelles distinctes. Ce principe fondamental repose sur la manipulation des plastiques thermosensibles, leur donnant la forme souhaitée. Les matériaux thermoplastiques sont d’abord exposés à une source de chaleur contrôlée, ce qui les rend malléables. Une fois suffisamment chauffés, ces matériaux sont étirés sur un moule méticuleusement conçu.
Une force externe, sous vide ou sous pression, est appliquée pour s’assurer que le plastique se conforme parfaitement à ce moule. Cette force garantit la précision, en veillant à ce que la feuille de plastique adhère fermement à chaque contour et détail du moule.
La polyvalence de cette méthode est vraiment louable. Non seulement elle permet de travailler avec un large éventail de matériaux thermoplastiques, mais ses applications couvrent divers secteurs. Une fois que le matériau thermoplastique a atteint sa forme finale, les étapes suivantes impliquent un ébarbage et une finition de précision. Ces procédures de postformage sont adaptées aux besoins spécifiques de l’utilisateur final, démontrant encore davantage la capacité d’adaptation du thermoformage.
Comment fonctionne le thermoformage ?
Étape 1 – Sélection des matériaux
Il est essentiel de choisir le bon type de plastique qui répond aux contraintes spécifiques du produit final. Divers facteurs, notamment la durabilité, la flexibilité et l’utilisation prévue du produit, guident cette sélection. Que ce soit pour le thermoformage en feuille mince, généralement utilisé dans les emballages, ou le thermoformage en feuille plus épaisse pour des composants plus importants, le choix du matériau est primordial.
Étape 2 – Chauffage et répartition uniforme de la température
Après la sélection du matériau, la feuille de plastique subit un processus de chauffage. Il est essentiel d’obtenir une distribution uniforme de la température sur toute la feuille. Toute variation peut entraîner des défauts ou des faiblesses dans le produit final. L’essence du thermoformage réside dans la malléabilité des plastiques lorsqu’ils sont chauffés. Par conséquent, le maintien d’une température constante garantit la malléabilité du plastique, ce qui facilite un moulage sans soudure.
Les méthodes utilisées pour le chauffage varient, mais elles visent toutes à assurer une température uniforme. La convection, le rayonnement et le chauffage par contact sont des pratiques standards, chacune avec ses avantages. La technique choisie dépend souvent du type de plastique et du thermoformage de jauge spécifique utilisé.
Le chauffage uniforme ne consiste pas seulement à atteindre la température souhaitée, mais aussi à s’assurer que cette chaleur est répartie uniformément, évitant ainsi les points chauds et les défauts qui en résultent.
Étape 3 – Moulage
Avec une feuille de plastique uniformément chauffée en main, la phase suivante est le moulage. Les moules de thermoformage sont essentiels pour façonner le plastique dans la structure tridimensionnelle souhaitée. Compte tenu de la diversité des produits créés par thermoformage, de nombreux types et procédés de moulage existent. Les moules sont généralement en aluminium.
Deux méthodes principales dominent le processus de moulage : le formage sous vide et le formage sous pression. Dans le formage sous vide, après avoir placé le plastique sur le moule, un vide aspire l’air, forçant le plastique à se conformer aux contours du moule. Inversement, le formage sous pression utilise de l’air comprimé pour pousser le plastique contre le moule, offrant des finitions plus détaillées et texturées.
Étape 4 – Refroidissement et ébarbage
Après le processus de moulage, le produit thermoformé n’est pas encore complet. Le refroidissement est essentiel pour garantir que le plastique conserve sa forme nouvellement acquise. Le plastique doit refroidir uniformément pour éviter toute déformation. Selon la taille du produit et le type de plastique, l’air ou l’eau peuvent accélérer le processus de refroidissement.
Une fois refroidi, le produit subit une opération d’ébarbage. La matière excédentaire, qui ne fait pas partie du produit final, est éliminée. Des techniques d’ébarbage avancées, souvent automatisées, sont utilisées pour garantir la précision. La découpe au laser ou la découpe à l’emporte-pièce, entre autres, sont couramment utilisées en fonction de la complexité du produit et du volume de production.
Matériaux de thermoformage
Il est essentiel de comprendre la variété des matériaux utilisés dans le thermoformage, car chacun offre des caractéristiques uniques adaptées à différentes applications. Le choix du matériau dépend souvent des propriétés et de la fonctionnalité souhaitées du produit final.
Matériaux les plus couramment utilisés pour le thermoformage
- PVC/Acrylique : Ce matériau est largement utilisé, en particulier dans les boîtiers d’équipements contenant des microprocesseurs. La résistance inhérente du PVC/Acrylique et sa capacité à répondre aux normes strictes d’inflammabilité UL ajoutent à son attrait. De plus, son adaptabilité s’étend également à l’esthétique ; il peut être fabriqué dans de nombreuses couleurs et textures pour répondre à des contraintes de design spécifiques.
- PS (Polystyrène) : Le polystyrène, ou polyphényléthène, est un polymère thermoplastique réputé pour ses propriétés d’isolation électrique. En tant que thermoplastique, il se ramollit à la chaleur et peut être remodelé, permettant ainsi d’être réutilisé. Sa résistance chimique aux acides et aux bases en fait un matériau polyvalent dans diverses applications, notamment les emballages de protection et l’isolation.
- PET (polyéthylène téréphtalate) : le PET est un incontournable dans l’univers des emballages thermoformés, des fibres synthétiques et de la production de bouteilles. Reconnu pour sa résistance et sa durabilité, le PET nécessite un séchage après le moulage, une étape cruciale pour assurer sa stabilité et conserver sa forme. Son utilisation généralisée dans les contenants d’aliments et de boissons met en évidence sa sécurité et sa fiabilité.
- PP (polypropylène) : Le polypropylène (PP) est réputé pour sa résistance à la fatigue et sa stabilité thermique, ce qui le rend essentiel dans les pièces automobiles, les biens de consommation et les charnières souples. Sa capacité unique à supporter des flexions continues sans se rompre est une propriété cruciale. De plus, sa résistance à l’humidité, aux acides et aux solvants rend le PP idéal pour les récipients et les tuyauteries, ainsi que pour les équipements médicaux et de laboratoire.
- PEBD (polyéthylène basse densité) : Le PEBD, caractérisé par sa flexibilité et sa résilience, est la pierre angulaire de la création de produits qui exigent un équilibre entre souplesse et résistance. Sa résistance à l’humidité et aux produits chimiques le rend idéal pour les emballages alimentaires et les récipients de laboratoire. De plus, sa résistance aux basses températures garantit des performances fiables dans des applications allant de l’emballage d’aliments congelés aux tubes flexibles et aux films agricoles.
- PEHD (polyéthylène haute densité) : Le PEHD, connu pour sa robustesse, fait partie intégrante de la fabrication de biens durables tels que les casques de protection et les tuyauteries résistantes à la corrosion. Sa résilience environnementale, associée à un rapport résistance-densité élevé, en fait un choix idéal pour des applications exigeantes, garantissant longévité et fiabilité dans des produits allant du mobilier d’extérieur aux contenants de stockage.
- PC (Polycarbonate) : Le polycarbonate (PC) se distingue par sa résistance aux chocs et sa clarté optique, ce qui en fait un choix privilégié pour les équipements de sécurité, comme le verre pare-balles, et dans les composants automobiles. Sa polyvalence s’étend aux supports électroniques, comme les DVD et les disques Blu-ray, démontrant sa capacité à maintenir la transparence et la durabilité sous contrainte.
- PMMA (polyméthacrylate de méthyle) : Le PMMA, célèbre pour sa clarté vitreuse et sa résistance aux UV, est largement utilisé dans les lentilles optiques, les aquariums et les éléments architecturaux. Son excellente transmission de la lumière et sa résistance aux intempéries en font un choix privilégié pour les applications extérieures, démontrant sa capacité à conserver clarté et force dans des environnements divers.
- ABS (Acrylonitrile Butadiène Styrène) : l’ABS englobe un large spectre de résines, ce qui le rend polyvalent dans de nombreuses applications. Il est robuste et durable et peut également être formulé pour respecter les normes d’inflammabilité UL. Cette adaptabilité fait de l’ABS un favori dans diverses industries.
Tableau de comparaison des matériaux de thermoformage
Nom du matériau | Stabilité thermique | Résistance aux produits chimiques | Résistance aux UV | Rigidité | Coût |
PVC | Médiocre | Médiocre | Passable | Variable | Moyenne |
PS | Passable | Médiocre | Médiocre | Élevé | Faible |
PET | Passable | Bien | Médiocre | Variable | Élevé |
PP | Médiocre | Excellent | Médiocre | Variable | Faible |
LDPE | Médiocre | Médiocre | Médiocre | Faible | Faible |
HDPE | Passable | Bien | Passable | Élevé | Faible |
PC | Élevé | Bien | Passable | Faible | Élevé |
PMMA | Médiocre | Bien | Passable | Élevé | Faible |
ABS | Passable | Médiocre | Médiocre | Élevé | Moyenne |
Le domaine des matériaux de thermoformage est vaste et varié. En alignant les propriétés du matériau sur les contraintes du projet, on peut exploiter pleinement le potentiel du thermoformage, assurant des résultats de haute qualité pour le produit final.
Types de thermoformage
Comprendre les processus de thermoformage est crucial pour choisir la bonne méthode pour une application donnée. Deux techniques principales dominent : le thermoformage sous vide et le thermoformage sous pression. Chacune présente ses avantages, adaptés à des contraintes et à des produits spécifiques.
Thermoformage sous vide
Précédant de nombreux traitements plastiques modernes, le processus de formage sous vide se distingue comme une méthode fondamentale et couramment utilisée. Son influence sur les produits quotidiens est profonde et reste essentielle pour façonner le plastique en articles durables.
Comment fonctionne le thermoformage sous vide :
- Une feuille de plastique est initialement assouplie par chauffage contrôlé
- Cette feuille chauffée et malléable s’étend ensuite sur un moule prédéterminé
- En utilisant un vide, la feuille est serrée fermement contre le moule, assurant une conformité précise de la forme
- La feuille désormais formée se détache du moule lors du refroidissement, conservant sa nouvelle forme
Avec les progrès, le formage sous vide contemporain intègre désormais des contrôleurs pneumatiques, hydrauliques et thermiques complexes. Cette sophistication accélère la production et affine la précision des produits finaux.
Thermoformage sous pression
Une innovation plus contemporaine, le formage sous pression, est une approche affinée de la mise en forme des plastiques. Le procédé se distingue du formage sous vide non pas par le produit final, mais par la technique employée pour y parvenir.
Fonctionnement du thermoformage sous pression :
- Le vide et la pression d’air sont utilisés simultanément, forçant la feuille de plastique dans le moule
- La feuille de plastique subit un chauffage jusqu’à ce qu’elle atteigne un état pliable optimal
- Contrairement au formage sous vide, qui aspire l’air, le formage sous pression exerce une pression d’air. Cette action garantit que le plastique est poussé fermement dans les contours détaillés du moule
- Le mécanisme précis de stabilisation du plastique garantit la température optimale, facilitant la création de moules flexibles mais précis
L’attrait du thermoformage sous pression réside dans sa capacité à produire des composants avec des détails améliorés, des bords plus nets et une finition générale supérieure. Lorsqu’un projet exige de la complexité et de la précision, le thermoformage sous pression apparaît comme la méthode de choix.
Bien que les deux procédés de thermoformage soient essentiels dans l’industrie, leur application dépend des contraintes spécifiques du produit. Ces techniques, des articles ménagers aux composants industriels, jouent un rôle déterminant dans la fourniture de produits en plastique de qualité.
Avantages du thermoformage
Le thermoformage, un processus clé dans le domaine de la fabrication du plastique, présente plusieurs avantages. Ces avantages en font un choix privilégié pour les fabricants visant une production efficace, rentable et flexible. Voici un aperçu des avantages notables que ce processus offre :
- Rentabilité pour des séries de production moyennes : le thermoformage se démarque lorsqu’il s’agit de produire de grandes quantités. Sa simplicité et sa nature épurée signifient moins de pièces mobiles, ce qui réduit les coûts de maintenance. De plus, les moules utilisés sont relativement moins chers que ceux des autres procédés, ce qui en fait un choix plus économique pour la production à petite et moyenne échelle.
- Rapidité de production : La simplicité inhérente au processus garantit des cycles de production rapides. Contrairement aux méthodes alternatives, en particulier celles qui nécessitent des moules complexes ou des temps de durcissement prolongés, le thermoformage apparaît souvent comme l’option la plus rapide.
- Flexibilité du design et prototypage rapide : L’une des caractéristiques du thermoformage est sa polyvalence en matière de design. Les fabricants ne sont pas contraints par des structures de design rigides. Au lieu de cela, ils peuvent rapidement adapter et modifier les designs selon les besoins. Cette flexibilité s’étend également au prototypage.
- Efficacité en matière de gestion des déchets et de consommation d’énergie : le thermoformage est particulièrement efficace à la fois en termes de gestion des déchets matériels et d’utilisation de l’énergie. Les matériaux excédentaires provenant du processus de formage peuvent souvent être recyclés directement dans le cycle de production, réduisant ainsi le gaspillage. En outre, l’énergie nécessaire pour chauffer les feuilles de plastique lors du thermoformage est généralement inférieure à celle de nombreuses méthodes alternatives, ce qui contribue à réduire l’empreinte carbone et les coûts d’exploitation.
Limites du thermoformage
Alors que le thermoformage offre divers avantages, il a également des inconvénients. Reconnaître ces contraintes permet aux fabricants de prendre des décisions éclairées et d’optimiser leurs stratégies de production.
- Restrictions matérielles : tous les plastiques ne conviennent pas au processus de thermoformage. Certains matériaux n’ont pas les caractéristiques nécessaires pour se former efficacement sous l’effet de la chaleur et de la pression.
- Complexité du design des pièces : le thermoformage présente certaines contraintes pour les éléments de design complexes. Obtenir des géométries très détaillées ou complexes peut être difficile, contrairement à d’autres processus. Cette limitation signifie que les produits comprenant des composants extrêmement détaillés peuvent nécessiter des processus supplémentaires ou des méthodes de fabrication alternatives.
- Épaisseur et consistance des parois : l’un des principaux défis du thermoformage est de maintenir une épaisseur de paroi uniforme, en particulier avec des formes plus profondes ou des moules plus complexes. La nature du processus peut conduire à des parois plus minces dans certaines parties du produit formé. Cette incohérence peut affecter l’intégrité structurelle du produit et sa qualité globale.
Applications du thermoformage
La nature polyvalente du thermoformage se prête à diverses industries, offrant des solutions sur mesure pour répondre à des demandes spécifiques. Sa capacité à mouler des plastiques sous des formes et des structures variées change la donne dans de nombreux secteurs.
Industrie de l’emballage
Le thermoformage est un processus clé dans le secteur de l’emballage. La création de plateaux thermoformés garantit que les produits sont sécurisés pendant le transport, minimisant ainsi les dommages potentiels. De plus, principalement utilisés dans les emballages alimentaires et les produits pharmaceutiques, les blisters sont un témoignage de la précision du thermoformage, car ces emballages enveloppent étroitement des articles individuels, offrant protection et visibilité.
Les blisters double coque, un autre produit de thermoformage, sont des solutions d’emballage robustes, en particulier dans la vente au détail, protégeant les articles des contaminants externes.
Industrie automobile
L’industrie automobile exploite largement le thermoformage pour ses innombrables avantages. Les composants tels que les panneaux de porte et les tableaux de bord nécessitent une durabilité combinée à une finition raffinée. Le thermoformage facilite la création de ces composants, en veillant à ce qu’ils soient à la fois esthétiques et fonctionnels. Au fur et à mesure que les véhicules continuent d’évoluer, intégrant des technologies de pointe, la demande de composants moulés avec précision augmente.
Secteur de la santé
Dans une industrie où la précision et l’hygiène sont primordiales, le thermoformage joue un rôle important. L’emballage des appareils médicaux, essentiel au maintien de la stérilité, utilise souvent des plastiques thermoformés. Cela garantit que les appareils restent non contaminés et prêts à l’emploi en cas de besoin.
De plus, les plateaux d’instruments chirurgicaux, moulés pour contenir des outils spécifiques, illustrent la précision du thermoformage. Ces plateaux organisent la disposition des instruments et facilitent la stérilisation, mettant en évidence l’importance du processus dans les soins de santé.
Biens de consommation
Des jouets avec lesquels les enfants jouent aux récipients utilisés quotidiennement dans les ménages, l’influence du thermoformage dans le secteur des biens de consommation est vaste. Le processus permet la création de jouets durables, en veillant à ce qu’ils résistent à l’épreuve du temps. Les récipients, en revanche, bénéficient de la capacité du thermoformage à créer des joints étanches, en gardant le contenu frais. Compte tenu de la diversité des biens de consommation, le partenariat avec Xometry garantit la meilleure application des techniques de thermoformage.
Les applications du thermoformage s’étendent à tous les secteurs, répondant à des défis distincts avec des solutions sur mesure. Sa polyvalence lui permet de rester à la pointe du secteur de la fabrication.
Thermoformage vs moulage par injection
Le thermoformage et le moulage par injection sont chacune des méthodes de fabrication de plastique cruciales. Cependant, elles diffèrent fondamentalement par leur approche et leur application.
Le thermoformage consiste à chauffer une feuille de plastique jusqu’à ce qu’elle devienne malléable. Cette feuille ramollie est ensuite moulée sur une forme spécifique. C’est un processus idéal pour les grandes pièces et les productions de grande à moyenne série. Sa flexibilité, ses coûts d’outillage réduits et son adaptabilité rapide aux prototypes en sont les avantages. Cependant, il est généralement limité à des designs plus simples et génère souvent plus de déchets de matériaux.
En revanche, le moulage par injection force le plastique fondu dans un moule sous haute pression. Ce processus excelle dans la création de designs complexes et convient mieux aux productions en grande quantité. Les produits finaux offrent une qualité constante et des tolérances serrées. Le principal inconvénient est le coût d’outillage initial plus élevé, ce qui le rend moins économique pour les petites séries.
Moulage par injection | Thermoformage | |
Quantité | 50 – 1 000 000 | > 1 |
Échantillon | + d’1 mois | + d’1 mois |
Prototypage | ✔ | ✔ |
Production de gros volumes | ✔ | ✘ |
Fonctionnel | ✔ | ✔ |
Esthétique | ✔ | ✔ |
Géométries complexes | ✔ | ✘ |
Pièces colorées | ✔ | ✔ |
En choisissant entre ces méthodes, tenez compte de la complexité du produit, du volume de production et des contraintes budgétaires. Les deux processus ont leurs mérites, mais la décision dépend souvent des contraintes spécifiques du projet en question.
Passer des commandes de fabrication avec le thermoformage chez Xometry
Le processus de thermoformage est une méthode essentielle dans le domaine de la fabrication, offrant des solutions polyvalentes pour façonner divers matériaux. Son adaptabilité dans tous les secteurs, y compris l’automobile, le médical et l’emballage, met en évidence son caractère pratique.
Pour les entreprises à la recherche de solutions fiables pour la production à faible et moyen volume, Xometry offre des services de thermoformage de première qualité.
Comment(0)