La stampa a compressione è una pietra miliare tra i processi produttivi, in quanto fornisce un ottimo metodo per la realizzazione di componenti complessi con precisione e affidabilità. Questa tecnica versatile prevede l’uso del calore e della pressione per modellare le materie prime nelle forme desiderate, rendendola una scelta popolare in diversi settori.
Processo di stampa a compressione
I meccanismi fondamentali della stampa a compressione sono semplici. Le forze di compressione vengono applicate per modellare una carica di materiale deformabile che poi si indurisce attraverso la polimerizzazione prima della sua rimozione dallo stampo.
Il processo inizia con l’introduzione della carica di materiale nello stampo. Una potente pressa esercita quindi una forza sullo stampo, comprimendo la carica e riempiendo la cavità con il materiale.
Una volta che il materiale è stato completamente distribuito all’interno dello stampo, viene sottoposto ad un periodo di riposo. Durante questa fase, il calore e la pressione fanno sì che il materiale subisca una trasformazione chimica, indurendosi nella forma desiderata.
Dopo la polimerizzazione, la parte stampata a compressione viene accuratamente estratta dallo stampo. Qualsiasi materiale in eccesso, noto come bava, che potrebbe essere fuoriuscito durante il processo, viene rimosso durante la post-elaborazione.
Stampa a compressione vs. Stampa a iniezione
Nonostante le somiglianze con la stampa a iniezione, quella a compressione possiede una caratteristica distintiva. La stampa a compressione prevede la chiusura degli stampi attorno alla carica, mentre nella stampa a iniezione la carica viene iniettata in una cavità dello stampo chiusa.
Lo stampaggio a iniezione, spesso la scelta preferita per parti complesse, richiede tempi ciclo più brevi che lo rendono più rapido ed economico per la produzione su larga scala.
La stampa a compressione, essendo un processo a bassa pressione, offre costi di attrezzaggio ridotti, rendendolo ideale per progetti più semplici e cicli di produzione medio-piccoli.
Suggerimenti di progettazione per la stampa a compressione
Il modo in cui si progettano le parti per la stampa a compressione è molto meno complicato rispetto alla progettazione per quella ad iniezione, poiché non vi è quasi alcun ritiro, deformazione o cedimento da affrontare. Ma consigliamo di considerare le seguenti linee guida di progettazione:
Spessore delle pareti
Uno dei vantaggi che progettisti e ingegneri hanno quando lavorano con la stampa a compressione è la flessibilità dello spessore delle pareti. A differenza di molti altri processi produttivi, la stampa a compressione non impone restrizioni rigorose sullo spessore minimo o massimo delle pareti, aprendo la strada a una maggiore flessibilità di progettazione.
Nella stampa a compressione, è possibile ottenere pareti sia sottili che spesse all’interno della stessa parte senza compromettere l’integrità strutturale o l’accuratezza dimensionale del prodotto finale.
Sebbene questa sia un’importante libertà, l’attenta considerazione dello spessore delle pareti è ancora fondamentale. Può avere una grande influenza sul costo di una parte per via del maggiore tempo di polimerizzazione e dell’utilizzo di materiale associato alle parti con pareti spesse.
- Spessore della parete ottimale: 1,5 mm – 6 mm
- Spessore minimo della parete: 0,5 mm
- Spessore massimo della parete: + di 12 mm
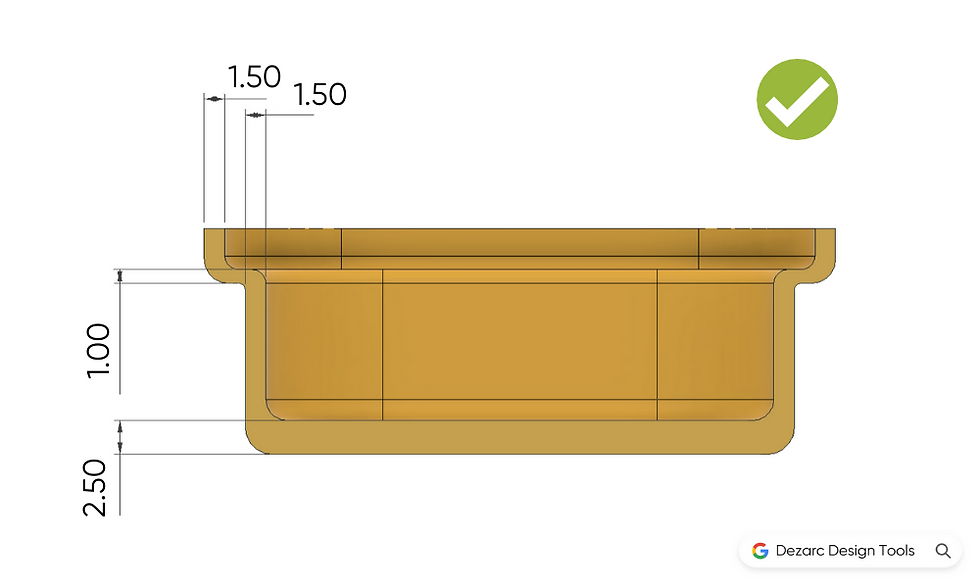
Sottosquadri
I sottosquadri – ovvero le rientranze inaccessibili dalle estremità aperte dello stampo – possono spesso complicare il processo di stampa poiché di solito richiedono azioni laterali o nuclei deformabili per l’espulsione.
Siccome la maggior parte dei componenti formati mediante stampa a compressione utilizzano materiali elastomerici come il silicone, è possibile realizzare sottosquadri senza aggiungere complesse caratteristiche meccaniche.
Tuttavia, quando si progettano parti stampate a compressione con sottosquadri emergono due fondamentali considerazioni:
- La fattibilità della realizzazione del sottosquadro tramite elettroerosione o lavorazione CNC. Se ciò non è fattibile, potrebbe essere necessario uno stampo multiparte preassemblato, che aumenta i costi di attrezzaggio e riduce la durata degli utensili.
- La facilità di rimozione del pezzo dallo stampo. Se la parte non può essere rimossa senza causare danni o richiedere sforzi eccessivi, i costi di manodopera aumentano. Nello scenario peggiore, quando la parte non può essere rimossa senza provocare danni, il produttore potrebbe dover creare uno stampo più complesso. Ciò potrebbe comportare azioni laterali, una piastra intermedia o nuclei deformabili, che aumentano i costi degli stampi e riducono la durata degli stessi.
La possibilità o meno di rimuovere una parte dallo stampo dipenderà da una serie di fattori specifici dell’applicazione, come le proprietà del materiale e la geometria della parte. È sempre meglio contattare il proprio fornitore per chiedere la sua opinione durante la progettazione ed evitare eventuali problemi in futuro.
Angolo di sformo
Nello stabilire lo sformo minimo per una parte, la rigidità del materiale previsto è la principale considerazione da fare. È del tutto fattibile stampare componenti elastomerici con angoli di sformo pari a zero o addirittura negativi.
Il compromesso è il costo della manodopera associato all’estrazione della parte dallo stampo. Il Design for Manufacture (DFM) riguarda l’ottimizzazione di ogni fase del processo di produzione, dall’attrezzaggio fino all’assemblaggio.
Incorporando lo sformo nelle parti è possibile semplificare il processo di rimozione, con conseguente riduzione dei costi di produzione.
Angoli di sformo suggeriti:
- Per pareti di spessore inferiore a 25 mm: si consiglia un angolo di 1 – 2°
- Per pareti di altezza superiore a 25 mm: si consiglia un angolo di 2 – 4°
Innesti a scatto
Potremmo scrivere un’intera guida alla progettazione solo sui vari tipi di incastri e su come progettarli, ma in questa sezione tratteremo solo le nozioni di base.
Giunti a scatto a sbalzo: l’accoppiamento a scatto a sbalzo convenzionale viene raramente utilizzato in combinazione con materiali elastomerici.
Giunti a scatto anulari: questi tipi di accoppiamenti a scatto sono perfettamente adatti per componenti realizzati con materiali elastomerici, una caratteristica che deriva dalla flessibilità intrinseca del materiale. Come suggerisce il nome sono caratterizzati dalla loro struttura circolare o ad anello.
Gli accoppiamenti a scatto anulari utilizzano le proprietà elastiche del materiale per consentire il montaggio e lo smontaggio. Quando le parti vengono accostate, il bordo sporgente dell’accoppiamento a scatto si deforma per consentire l’assemblaggio e poi rimbalza una volta in posizione, tenendo insieme saldamente le parti.
Stampaggio a inserti
Una caratteristica comune di questo settore, lo “stampaggio a inserti”, prevede il posizionamento di una parte prefabbricata, spesso metallica, all’interno di uno stampo. Tale stampo viene successivamente riempito con materiale di stampa che, solidificandosi, crea un componente che integra la parte inserita.
Per uno stampaggio ad inserti efficace con la stampa a compressione, è necessario affrontare due considerazioni chiave:
- L’impatto delle forze di compressione: è necessaria una forza significativa per garantire il completo riempimento della cavità. Se i materiali incapsulati sono delicati, potrebbero subire danni per via di queste forze ripetute.
- Mantenimento della posizione dell’inserto: durante il processo di stampa, garantire la posizione dell’inserto è fondamentale. Questo si ottiene generalmente utilizzando perni di stampi a compressione che trattengono l’inserto esternamente, creando una sezione che rimane vuota.
A condizione che si tenga debitamente conto di questi punti, la stampa a compressione può essere utilizzata per racchiudere un’ampia gamma di elementi, dagli inserti filettati alle antenne, all’interno di una resina termoindurente.
Inserti comuni:
- Inserti filettati: generalmente realizzati in ottone o acciaio. Consentono l’uso ripetuto di filetti durevoli nelle parti in gomma
- Pesi: i pesi vengono spesso aggiunti alle parti stampate per scopi funzionali o per aggiungere una sensazione di qualità superiore
- Schede di circuiti stampati (PCB): queste schede elettroniche possono essere incapsulate in materiale per formare gruppi elettronici durevoli e impermeabili
- Cablaggio: il cablaggio elettrico può essere racchiuso nel materiale per ottenere cablaggi durevoli
- Pulsanti: è possibile formare un foglio elastomerico di più pulsanti per controllare i sistemi elettrici
Texture
La texture non è solo una questione estetica: è una caratteristica funzionale significativa che può influenzare drasticamente le prestazioni del prodotto. Che stiate cercando di migliorare il grip, camuffare i segni di produzione o creare un determinato effetto visivo, la texture gioca un ruolo fondamentale nella progettazione dei componenti.
Quando si tratta di definire la struttura di una parte stampata, l’industria generalmente fa riferimento a due standard principali: gli standard della Society of the Plastics Industry (SPI) e gli standard dell’Associazione degli ingegneri tedeschi (VDI).
Lo stampaggio a compressione consente una riproduzione lucente delle texture dell’intera gamma SPI e VDI, dalle finiture grezze per elettroerosione a quelle lucide diamantate.
La nostra gamma di campioni di durezza di elastomeri stampati a compressione presenta 4 tipi di zone di texture SPI che dimostrano brillantemente quanto lo stampaggio a compressione possa riprodurre bene le texture.
Mini-guidatexture SPI:
- Lucida- SPI A1-3
- Semi-lucida – SPI B1-3
- Opaca- SPI C1-3
- Texturizzata – SPI D1-3
Selezione dei materiali per la stampa a compressione
Ecco le due principali categorie di materiali utilizzati nella stampa a compressione:
- Elastomeri: Qualsiasi materiale gommoso in grado di recuperare la sua forma originale dopo una deformazione significativa
- Termoindurente: I polimeri termoindurenti sono materiali resistenti al calore che subiscono una reazione chimica irreversibile una volta polimerizzati, dando vita a una struttura rigida che mantiene la sua forma anche a temperature elevate.
Elastomeri termoindurenti
Questa è la categoria più comune di materiali stampati a compressione e viene utilizzata in una vasta gamma di applicazioni, dagli O-ring e guarnizioni ai contenitori per alimenti. Poiché i materiali termoindurenti non si sciolgono, sono perfetti per applicazioni di sigillatura ad alta temperatura.
La durezza (o morbidezza) degli elastomeri viene misurata da uno strumento chiamato durometro. Esso misura la resistenza di un materiale all’impronta. La scala Shore A viene utilizzata per comunicare la durezza richiesta dei siliconi.
In genere le parti in elastomero stampato a compressione rientrano tra lo Shore A20 e lo Shore A80 con A20 simile a una soletta in gel e lo Shore A80 simile ad un battistrada. Per avere un’idea pratica della durezza dell’elastomero, date un’occhiata al nostro kit di campioni.
- Silicone: il silicone è un elastomero termoindurente comunemente usato. Non solo è resistente alla temperatura, ma è anche resistente all’abrasione, agli agenti chimici, adatto agli alimenti e biocompatibile
- Nitrile: un materiale molto comune nelle applicazioni di tenuta industriale grazie alla sua resistenza all’olio
- Viton: utilizzato in applicazioni automotive ad alta temperatura grazie alla sua gomma in stirene-butadiene resistente ai combustibili fossili; utilizzato anche in applicazioni impermeabili grazie alla sua resistenza all’acqua
Materie plastiche termoindurenti
Lo stampaggio a compressione consente la formazione di materiali compositi resistenti attraverso la combinazione di resina polimerica, fibre, stabilizzanti e riempitivo.
Esistono due principali resine composite utilizzate nell’industria automobilistica, note come sheet moulding compound (SMC) e bulk moulding compound (BMC).
Resine termoindurenti comuni:
- Resina epossidica: Ottima resistenza meccanica
- Poliestere: Eccellente resistenza chimica
- Poliuretano: Può essere sintetizzato per produrre un’ampia gamma di caratteristiche del materiale
L’uso di materiali termoindurenti è un argomento controverso poiché questi tipi di plastica non possono essere facilmente riciclati o smaltiti in modo sostenibile. Quando l’applicazione lo consente, dovrebbero essere sostituite da plastiche più ecosostenibili.
Conclusione
In conclusione, comprendere e implementare strategie di progettazione efficaci nella stampa a compressione può avere un impatto significativo sull’efficienza e sulla qualità dei processi produttivi. Concentrandosi sui principi di progettazione e sulla scelta dei materiali, ingegneri e produttori possono sfruttare tutto il potenziale di questa tecnica versatile.
Comment(0)