Le moulage par compression constitue une pierre angulaire des processus de fabrication, fournissant une méthode robuste pour fabriquer des composants complexes avec précision et fiabilité. Cette technique polyvalente implique l’utilisation de la chaleur et de la pression pour façonner des matières premières dans les formes souhaitées, ce qui en fait un choix populaire dans diverses industries.
Processus de moulage par compression
La mécanique fondamentale du moulage par compression est simple. Des forces de compression sont appliquées pour former une charge de matériau déformable qui durcit ensuite par maturation avant son retrait du moule.
Le processus commence par l’introduction de la charge de matériau dans le moule. Une presse puissante applique ensuite une pression sur le moule, comprimant la charge et remplissant la cavité du moule avec du matériau.
Une fois que le matériau a été entièrement réparti dans le moule, il est ensuite soumis à une période de maturation. Au cours de cette étape, la chaleur et la pression font subir au matériau une transformation chimique, le durcissant dans la forme prévue.
Après cette phase de maturation, la pièce moulée par compression est soigneusement extraite du moule. Tout excès de matériau, connu sous le nom de flash, qui peut s’être infiltré au cours du processus, est éliminé lors de l’étape de finition.
Moulage par compression vs Moulage par injection
Malgré des similitudes avec le moulage par injection, le moulage par compression présente une caractéristique distinctive. Le moulage par compression exige que les moules soient fermés autour de la charge, tandis que lors du moulage par injection, la charge est injectée dans une cavité de moule fermée.
Le moulage par injection, souvent un choix privilégié pour les pièces complexes, nécessite des temps de cycle plus courts, ce qui le rend plus rapide et plus rentable pour la production à grande échelle.
Le moulage par compression étant un processus à basse pression, il offre des coûts d’outillage réduits, ce qui le rend idéal pour des designs plus simples et des séries de production petites à moyennes.
Conseils de design pour le moulage par compression
La conception de pièces pour le moulage par compression est nettement moins compliquée que pour le moulage par injection, car il n’y a presque pas de problèmes de rétrécissement, de gauchissement ou d’affaissement. Mais nous vous recommandons de prendre en compte les directives suivantes en matière de design :
Épaisseur de paroi
L’un des avantages que les designers et les ingénieurs ont lorsqu’ils utilisent le moulage par compression est la flexibilité de l’épaisseur des parois. Contrairement à de nombreux autres processus de fabrication, le moulage par compression n’impose pas de restrictions strictes sur l’épaisseur minimale ou maximale de la paroi, ouvrant la voie à une flexibilité de design accrue.
Dans le moulage par compression, il est possible d’obtenir à la fois des parois minces et des parois épaisses sur la même pièce sans compromettre l’intégrité structurelle ou la précision dimensionnelle du produit final.
Bien que cette flexibilité soit libératrice, porter une attention particulière à l’épaisseur de la paroi est toujours crucial. Cela peut avoir une grande influence sur le coût d’une pièce en raison du temps de durcissement accru et de l’utilisation de matériaux associés aux pièces à paroi épaisse.
- Épaisseur optimale de la paroi : de 1,5 à 6 mm
- Épaisseur minimale de la paroi : 0,5 mm
- Épaisseur de paroi maximale : + de 12 mm
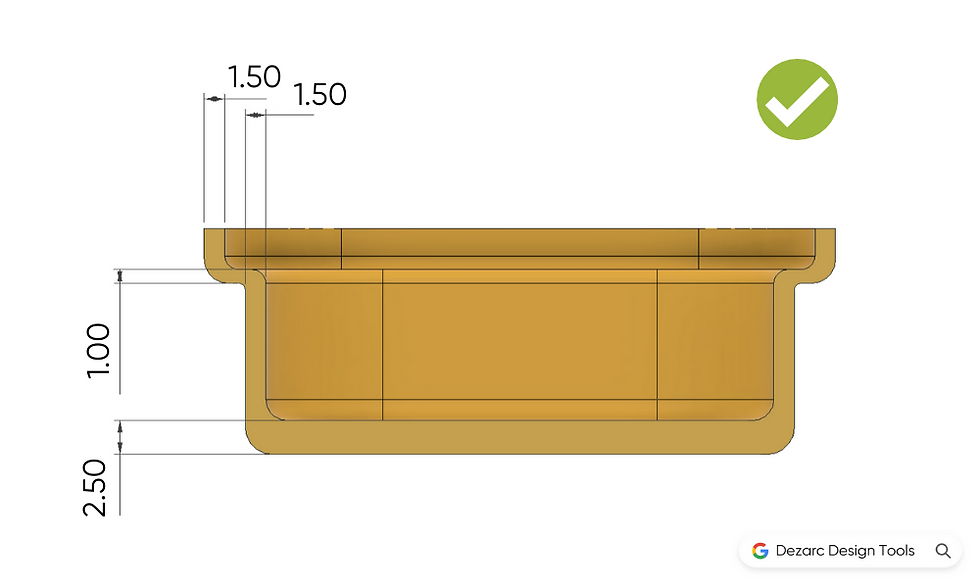
Contre-dépouilles
Les contre-dépouilles – des évidements inaccessibles depuis les extrémités ouvertes du moule – peuvent souvent compliquer le processus de moulage car elles nécessitent généralement des actions latérales ou des noyaux rétractables pour l’éjection.
Étant donné que la plupart des pièces formées par moulage par compression utilisent des matériaux élastomères comme le silicone, les contre-dépouilles sont réalisables sans ajouter de caractéristiques mécaniques complexes.
Cependant, deux considérations critiques se posent lors du design de pièces moulées par compression avec contre-dépouilles :
- La faisabilité de la formation de la contre-dépouille par usinage EDM ou CNC. Si cela n’est pas possible, un outil de moulage en plusieurs parties préassemblé peut être nécessaire, ce qui augmente les coûts d’outillage et réduit la durée de vie de l’outillage.
- La facilité à retirer la pièce du moule. Si la pièce ne peut pas être retirée sans causer de dommages ou nécessiter des efforts excessifs, les coûts de main-d’ œuvre augmentent. Dans le pire des cas, lorsque la pièce ne peut pas être retirée du tout sans causer de dommages, le fabricant d’outillage peut avoir besoin de créer un moule plus complexe. Cela peut consister à appliquer des actions latérales, utiliser une plaque centrale ou des noyaux pliables, ce qui augmente les coûts d’outillage et réduit la durée de vie de l’outillage.
La possibilité de retirer ou non une pièce du moule dépendra de certains facteurs spécifiques à votre application, tels que les propriétés du matériau et la géométrie de la pièce. Il est toujours préférable de demander l’avis de votre fournisseur pendant le processus de design afin d’éviter tout problème ultérieur.
Angle de dégagement
Lors de l’établissement de l’angle de dégagement minimum d’une pièce, la rigidité du matériau prévu est la considération principale. Il est tout à fait possible de mouler des composants élastomères avec un angle de dégagement nul ou même négatif.
La contrepartie est la dépense de main-d’ œuvre associée à l’extraction de la pièce du moule. Le DFM (Design pour la fabrication) consiste à optimiser chaque étape du processus de fabrication, de l’outillage à l’assemblage.
En intégrant l’angle de dégagement dans les pièces, le processus de retrait peut être simplifié, ce qui permet de réduire les coûts de fabrication.
Angles de dégagement suggérés :
- Pour les parois d’une épaisseur de moins de 25 mm : un angle de dégagement de 1 à 2° est recommandé
- Pour les parois de plus de 25 mm : un angle de dégagement de 2 à 4° est conseillé
Fixations par encliquetage
Nous pourrions écrire un guide de design complet sur les différents types d’encliquetage et sur la façon de les concevoir, mais dans cette section, nous allons nous contenter de couvrir les bases.
Fixations par encliquetage en porte-à-faux : La fixation par encliquetage en porte-à-faux conventionnelle est rarement utilisée en conjonction avec des matériaux élastomères.
Fixations par encliquetage annulaires : Ces types de fixations par encliquetage conviennent parfaitement aux composants fabriqués à partir de matériaux élastomères, une caractéristique qui découle de la flexibilité inhérente du matériau. Comme leur nom l’indique, ils se caractérisent par leur structure circulaire ou annulaire.
Les fixations par encliquetage annulaires utilisent les propriétés élastiques du matériau pour permettre le montage et le démontage. Lorsque les pièces sont poussées ensemble, le bord saillant de l’encliquetage se déforme pour permettre l’assemblage, puis rebondit une fois qu’il est en place, maintenant solidement les pièces ensemble.
Moulage par insertion
Une caractéristique courante dans l’industrie du moulage, le « moulage par insertion », implique le positionnement d’une pièce préfabriquée, souvent métallique, dans un moule. Ce moule est ensuite rempli d’un matériau de moulage qui, lors de la solidification, crée un composant intégrant la partie insérée.
Pour un moulage par insertion efficace avec moulage par compression, deux considérations clés doivent être prises en compte :
- L’impact des forces de compression : Une force importante est nécessaire pour assurer le remplissage complet de la cavité. Si les matériaux encapsulés sont délicats, ils peuvent subir des dommages en raison de ces forces répétées.
- Le maintien de la position de l’insert : Pendant le processus de moulage, la sécurisation de la position de l’insert est cruciale. Cette sécurisation est généralement réalisée à l’aide de broches de moules de compression qui maintiennent l’insert à l’extérieur, conduisant à une section qui reste non remplie.
À condition que ces points soient dûment pris en compte, le moulage par compression peut être utilisé pour envelopper une large gamme d’éléments – des inserts filetés aux antennes – dans une résine thermodurcissable.
Inserts courants :
- Inserts filetés : généralement en laiton ou en acier. Ils permettent l’utilisation répétée de filetages durables dans des pièces en caoutchouc
- Poids : des poids sont fréquemment ajoutés aux pièces moulées à des fins fonctionnelles ou pour apporter une sensation de qualité supérieure
- Cartes de circuits imprimés (PCB) : Ces cartes électroniques peuvent être encapsulées dans un matériau pour former des assemblages électroniques durables et imperméables
- Câblage : Le câblage électrique peut être encapsulé dans un matériau pour former des faisceaux de câbles durables
- Boutons : une feuille élastomère de plusieurs boutons peut être formée pour contrôler les systèmes électriques
Texture
La texture n’est pas seulement une question d’esthétique, c’est une caractéristique fonctionnelle importante qui peut affecter considérablement les performances du produit.
Que vous cherchiez à améliorer l’adhérence, à camoufler des marques de fabrication ou à créer un certain effet visuel, la texture joue un rôle central dans le design des composants.
Lorsqu’il s’agit de définir la texture d’une pièce moulée, l’industrie se réfère généralement à deux normes principales : les normes SPI de la Society of the Plastics Industry (Société de l’industrie des plastiques en français) et les normes VDI de l’Association of German Engineers (Association des ingénieurs allemands en français).
Le moulage par compression permet une reproduction brillante de la gamme complète de textures SPI et VDI, des finitions EDM rugueuses aux finitions diamantées brillantes.
Notre gamme d’échantillons de dureté en élastomère moulé par compression comprend 4 types de zones de texture SPI qui montrent brillamment à quel point le moulage par compression peut reproduire les textures.
Guide sur la texture SPI :
- Brillant – SPI A1-3
- Semi-brillant – SPI B1-3
- Matt – SPI C1-3
- Texturé – SPI D1-3
Sélection du matériau de moulage par compression
Voici les deux principales catégories de matériaux utilisés pour le moulage par compression :
- Élastomère : Tout matériau caoutchouteux capable de retrouver sa forme d’origine après une déformation importante
- Thermodurcissable : Les polymères thermodurcissables sont des matériaux résistants à la chaleur qui subissent une réaction chimique irréversible lorsqu’ils sont durcis, ce qui donne une structure rigide qui conserve sa forme même à des températures élevées.
Élastomères thermodurcissables
Il s’agit de la catégorie la plus courante de matériaux moulés par compression et est utilisée dans une gamme d’applications allant des joints toriques et des joints d’étanchéité aux contenants de qualité alimentaire. Parce que les thermodurcissables ne fondent pas, ils sont parfaits pour les applications d’étanchéité à haute température.
La dureté (ou la souplesse) des élastomères est mesurée à l’aide d’un outil appelé duromètre. Le duromètre mesure la résistance d’un matériau à l’indentation. L’échelle Shore A est utilisée pour communiquer la dureté requise des silicones.
En règle générale, les pièces en élastomère moulées par compression se situent entre Shore A20 et Shore A80, Shore A20 étant similaire à une semelle intérieure en gel et Shore A80 à bande de roulement de pneu. Pour avoir une idée concrète de la dureté d’un élastomère, consultez notre kit d’échantillons.
- Silicone : Le silicone est un élastomère thermodurcissable couramment utilisé. Non seulement il est résistant à la température, mais il est également résistant à l’abrasion, résistant aux produits chimiques, sans danger pour les aliments et biocompatible
- Nitrile : Un matériau très courant dans les applications d’étanchéité industrielles en raison de sa résistance à l’huile
- Viton : utilisé dans les applications automobiles à haute température grâce à sa résistance au carburant caoutchouc styrène-butadiène : utilisé dans les applications humides en raison de sa résistance à l’eau
Plastiques thermodurcissables
Le moulage par compression permet la formation de matériaux composites solides grâce à la combinaison de résine polymère, de fibres, de stabilisants et de charges.
Il existe deux principales résines composites utilisées dans l’industrie automobile connues sous le nom de composé de moulage en feuille (SMC) et de composé de moulage en vrac (BMC).
Résines thermodurcissables courantes :
- Résine époxy : Excellente résistance mécanique
- Polyester : Excellente résistance chimique
- Polyuréthane : Peut être formulé pour produire un large éventail de caractéristiques de matériaux
L’utilisation de matériaux thermodurcissables est un sujet controversé car ces types de plastiques ne peuvent pas être facilement recyclés ou éliminés de manière durable. Lorsque l’application le permet, ils devraient être remplacés par des plastiques plus durables.
Conclusion
Pour conclure, la compréhension et la mise en œuvre de stratégies de design efficaces dans le moulage par compression peuvent avoir un impact significatif sur l’efficacité et la qualité des processus de fabrication. En se concentrant sur les principes de conception et la sélection des matériaux, les ingénieurs et les fabricants peuvent exploiter tout le potentiel de cette technique polyvalente.
Comment(0)