Druckguss ist ein Metallgussverfahren, in der Massenproduktion von hochwertigen, langlebigen Teilen weit verbreitet ist. Es ist dafür bekannt, dass es Bauteile mit einer hohen Maßgenauigkeit produziert, und es somit ideal für jene Branchen geeignet ist, in denen präzise und konsistente Teile benötigt werden, wie z.B. dem Automobilbau, der Luft- und Raumfahrt oder der Unterhaltungselektronik. Ganz egal, ob Sie also nach einer Herstellungsmethode für komplexe Formen suchen oder ein glattes Oberflächenfinish anstreben, so ist der Druckguss eine effiziente Lösung für die Produktion großer Stückzahlen von Metallteilen, während dabei sowohl enge Toleranzen als auch Leistungsanforderungen eingehalten werden können.
Was ist Druckguss?
Druckguss ist ein Fertigungsverfahren, das die Produktion von Metallteilen mit einem hohen Genauigkeitsgrad erlaubt. Während des Gussprozesses wird geschmolzenes Metall unter Druck in eine Gussform eingespritzt, in der es aushärtet, und die gewünschte Form erhält.
Diese Methode kann für die Produktion der verschiedensten Metallteile verwendet werden, und reicht von Zahnrädern über Motorblöcke bis hin zu Türgriffen und elektrischen Bauteilen.
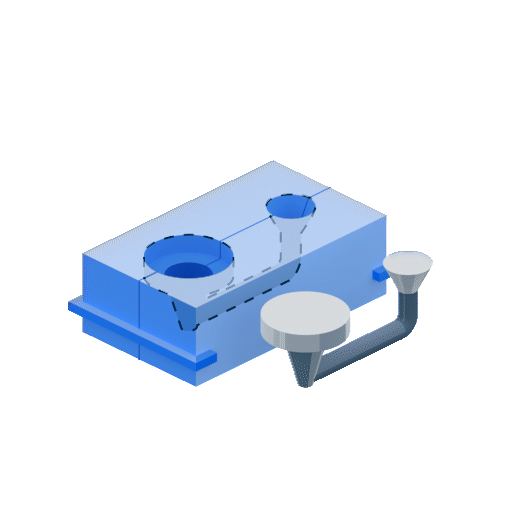
Der Druckguss wird für seine Fähigkeit geschätzt, Teile mit glatten Oberflächen und genauen Abmessungen zu produzieren. Darüber hinaus ist er relativ schnell und kosteneffizient, was den Druckguss zu einer Option für viele potenziellen Anwendungen macht.
Wie funktioniert der Druckguss?
Der Prozess des Druckgusses beinhaltet mehrere Schritte, inklusive des Formenbaus, der Metallvorbereitung, dem Einspritzvorgang, dem Gussvorgang und der abschließenden Oberflächenbehandlung.
Schritt 1 – Der Formenbau
Der erste Schritt des Druckgussverfahrens ist die Erschaffung einer Gussform (oder auch Druckgießform). Die Gussform besteht normalerweise aus Stahl oder Aluminium und wurde dazu entworfen, den hohen Temperaturen und Drücken während des Druckgießprozesses zu widerstehen.
Der Entwurfsprozess beginnt dabei mit der Entwicklung eines CAD-Designs des Bauteils und der darauf basierenden Gussform. Der Entwurf wird dann dafür verwendet, die eigentliche Druckgießform über CNC-Bearbeitung herzustellen.
Schritt 2 – Die Metallvorbereitung
Der nächste Schritt ist die Vorbereitung des Metalls für das Einspritzen. Das Metall ist typischerweise eine Legierung, wie mit Aluminium, Magnesium oder Zink. Das Metall wird in einem Hochofen geschmolzen und dann in eine sogenannte Kelle gegossen.
Schritt 3 – Der Einspritzprozess
Nachdem das Metall in die flüssige Phase übergegangen ist, wird es unter hohem Druck in die Gussform eingespritzt. Das geschmolzene Metall füllt dabei die Kavität bzw. den Hohlraum im Inneren der Gussform aus, kühlt ab und nimmt die gewünschte Form an.
Schritt 4 – Der Gussvorgang
Nachdem das Metall abgekühlt und ausgehärtet ist, wird die Form geöffnet und das Teil freigegeben. Dabei wird sichergestellt, dass das Teil vollständig ausgekühlt ist, um die Verletzungsgefahr beim Umgang damit zu minimieren.
Schritt 5 – Die Oberflächenbehandlung
Der letzte Schritt des Verfahrens ist die Oberflächenbehandlung. Diese spielt beim Druckguss eine entscheidende Rolle, da sie die Haltbarkeit und Funktionalität des Teils entscheidend beeinflussen kann. Zu standardmäßigen Oberflächenbehandlungen zählen das Eloxieren, die Pulverbeschichtung, Galvanik und noch viele mehr.
Arten des Druckgusses
Der Druckguss umfasst dabei verschiedene Verfahren, die alle für unterschiedliche Anforderungen seitens der Fertigung entwickelt wurden, und auf Faktoren wie den Materialtyp, die Produktionsgeschwindigkeit oder die Komplexität der Teile zugeschnitten sind. Die am häufigsten verwendeten Druckgussverfahren sind der Druckguss mit kalter und heißer Kammer, es gibt jedoch auch Varianten wie den Vakuum-, den Schwerkraft-, den Hochdruck- und den Niederdruckguss. Es folgt eine Übersicht der wichtigsten Arten des Druckgussverfahrens, einschließlich ihrer geeigneten Materialien und typischen Anwendungsgebiete:
Art des Druckgusses | Geeignete Materialien | Vorteile | Nachteile | Anwendungsgebiete |
Kaltkammerguss | Aluminium, Magnesium, Kupferlegierungen | hochfeste Teile, geeignet für Metalle mit hohem Schmelzpunkt | Langsamere Zykluszeiten durch Metalltransfer | Automobilbauteile (Motorblöcke, Getriebekästen) |
Warmkammerguss | Zink, Bleilegierungen | Schnelle Produktion, Metalle mit niedrigem Schmelzpunkt | Beschränkt auf Materialien mit niedrigerem Schmelzpunkt, Korrosionspotenzial | Elektrische Komponenten, Konsumgüter |
Vakuumguss | Aluminium, Magnesium, Zink | Verringerte Porosität, verbesserte mechanische Eigenschaften | Höhere Kosten, komplexerer Prozess erforderlich | Automobilteile, die eine hohe Festigkeit und enge Toleranzen erfordern (Motorteile) |
Kokillenguss | Aluminium, Zink, Kupfer | Bessere mechanische Eigenschaften als Sandguss, kostengünstige Werkzeuge | Geringere Präzision im Vergleich zum Hochdruckguss | Teile mittlerer Komplexität (Ventilkörper, Rohre) |
Hochdruckguss | Aluminium, Zink, Magnesium | Hervorragende Oberflächengüte, schnelle Produktion, hochpräzise | Höhere Werkzeugkosten, Porositätsprobleme | Automobil, Elektronik, Haushaltsgeräte |
Niedrigdruckguss | Aluminium | Bessere strukturelle Integrität, gut für große Teile | Langsamerer Prozessablauf, besser für geringere Produktionsmengen geeignet | Räder, große strukturelle Bauteile |
Kaltkammerguss
Im Kaltkammergussverfahren wird das geschmolzene Metall manuell in eine ungeheizte Einspritzkammer geschöpft. Diese wird dann unter hohem Druck über einen hydraulischen Kolben in die Druckgussform eingespritzt. Das Kaltkammerverfahren eignet sich in der Regel am besten für Metalle mit einem hohen Schmelzpunkt, wie Aluminium, Magnesium oder Kupferlegierungen, da diese Metalle die Anlage im Warmkammerverfahren beschädigen könnten.
Warmkammerguss
Im Warmkammerguss enthält die Anlage einen eingebauten Schmelzofen, in dem das Metall geschmolzen wird, bevor es direkt aus dem Schmelzofen in die Gussform eingespritzt wird. Ein Schwanenhalsmechanismus, der in die Metallschmelze eingetaucht wird, füllt sich mit dem Material und spritzt es dann unter Druck in die Matrize, die Gussform, ein. Das Warmkammerverfahren ist ideal für Metalle mit eher geringem Schmelzpunkt geeignet, wie Zink, Zinn oder Bleilegierungen, da das geschmolzene Metall dauerhaft in die Maschine eingeführt wird.
Vakuumguss
Im Vakuumguss liegt der Unterschied darin, dass in dieser Variante des Hochdruckgusses die Luft aus dem Hohlraum der Matrize evakuiert wird, bevor das heiße Metall eingespritzt wird. Das Vakuum verringert oder reduziert zumindest das Risiko, dass eingefangene Gase Teil des resultierenden Gussteils werden, wodurch sich eine verbesserte Dichte des Teils sowie verbesserte mechanische Eigenschaften ergeben. Das Vakuumverfahren hilft zudem dabei, die Porosität zu mindern, wodurch die daraus resultierenden Teile ideal für hohe Belastungen oder Drücke geeignet sind.
Kokillenguss
Im Kokillenguss, oder auch Schwerkraftguss, wird das geschmolzene Metall in eine Gussform oder Matrize gegossen, wobei nur die Schwerkraft eingesetzt wird. Das Metall fließt dabei in die Gussform und füllt den Hohlraum aus, bevor es abkühlte und erhärtet. Dabei wird kein externer Druck aufgewendet, und das Metall fließt allein durch die Schwerkraft in die Gussform. Das Verfahren ist dabei eher auf einfachere Teile ausgelegt und bietet dabei bessere mechanische Eigenschaften als im Sandguss.
Hochdruckguss
Der Hochdruckguss ist eines der am weitesten verbreiteten Druckgussverfahren. Bei dieser Methode wird geschmolzenes Metall mit sehr hohem Druck (i.d.R. zwischen 10 und 175 MPa) unter Verwendung eines Kolbens oder Stempels eingespritzt. Der hohe Druck stellt sicher, dass das gegossene Material alle Bereiche der Gussform ausfüllt, woraus sich ein sehr präzises und detailliertes Gussteil mit einer glatten Oberfläche ergibt. Der Prozessablauf ist dabei schnell, hochautomatisiert und für große Produktionsabläufe geeignet.
Niedrigdruckguss
Der Druckguss mit Niederdruck ist ein Verfahren bei dem das geschmolzene Metall langsam in und nur mit geringem Druck (0,1 bis 1 MPa) direkt aus einem Warmhalteofen unterhalb der Matrize eingepresst wird. Das Metall wird dabei durch ein Steigrohr in die Form gedrückt, wodurch eine reibungslose und kontrollierte Füllung des Hohlraum erreicht wird. Das Verfahren verringert die Turbulenzen und die Gaseinschlüsse, was zu hochwertigen Teilen mit wenigen Fehlern führt. Der Druckguss mit Niederdruck wird häufig für große Bauteile wie Aluminiumräder, Motorkomponenten und Strukturteile verwendet, bei denen die strukturelle Integrität und die Maßhaltigkeit entscheidend sind.
Geeignete Druckgussmaterialien
Zu Beginn eines Druckgussprojekts ist eine der kritischsten Entscheidungen die Wahl des richtigen Materials. Das Material muss sowohl in der Lage sein, die hohen Temperaturen und Drücke auszuhalten, die einen inhärenten Teil des Druckgusses darstellen. Gleichzeitig müssen aber auch die Funktions- und Leistungsanforderungen erfüllt werden, die die Endanwendungen stellt. Darüber hinaus ist es entscheidend, ein Material auszuwählen, das mit dem entsprechenden Druckgussverfahren kompatibel ist, da verschiedene Verfahren für manche Metalle besser geeignet sind.
Angesichts der Komplexität dieser Faktoren kann die Zusammenarbeit mit einem erfahrenen Partner für den Druckguss dabei helfen, sicherzustellen, dass Sie die bestmögliche Entscheidung auf Grundlage der einzigartigen Ansprüche Ihres Projekts treffen. Unter der breiten Palette der für das Verfahren verfügbaren Materialien, sind es insbesondere Aluminium, Magnesium sowie Zinklegierungen, die am häufigsten aufgrund ihrer Festigkeit, ihres geringen Gewichts und ihrer Vielseitigkeit eingesetzt werden.
Es folgt eine Gegenüberstellung der am häufigsten verwendeten Materialien, zusammen mit ihren Schlüsseleigenschaften und häufigsten Anwendungen:
Druckgussmaterial | Legierungsbeispiele | Schlüsseleigenschaften | Anwendungsgebiete |
Aluminium-legierungen | A380, A383, ADC12 | leicht, korrosionsbeständig, hochfest, exzellent maschinell bearbeitbar | Automobilteile, Komponenten für die Luft- und Raumfahrt, Unterhaltungselektronik |
Magnesium-legierungen | AZ91D, AM60B, AS41B | Ultraleicht, gutes Verhältnis von Festigkeit zu Gewicht, mäßige Korrosionsbeständigkeit | Leichte Automobilteile, Elektronik, Luft- und Raumfahrt |
Zinklegierungen | Zamak 3, Zamak 5 | Exzellente Gusseigenschaften, hochpräzise, gute elektrische Leitfähigkeit | Elektrische Komponenten, kleine Konsumgüter, Automobilteile |
Kupferlegierungen | Messing (C85700), Bronze | Hohe Korrosionsbeständigkeit, exzellente thermische und elektrische Leitfähigkeit | Sanitärarmaturen, elektrische Steckverbinder, Industriemaschinen |
Bleilegierungen | Blei, Zinn-Blei-Legierungen | Dicht, hervorragende Abschirmeigenschaften, leicht zu gießen | Batteriekomponenten, Strahlenschutz, kleine komplizierte Teile |
Vorteile des Druckgusses
Wenn es um die Massenproduktion von Metallteilen geht, so ist der Druckguss eine der effizientesten und kosteneffizientesten Methoden. Er ist ein Prozess, der bereits seit Jahrhunderten bekannt ist, und dennoch hat er gerade in jüngster Zeit an Popularität gewonnen, weil die Hersteller immer intensiver nach Wegen suchen, um die Produktionskosten zu vermindern.
Hier sind einige Vorteile des Druckgusses:
- Komplexe Formen: Der Druckguss ist ein Verfahren, das komplexe Formen mit engen Toleranzen produzieren kann.
- Vielfältigkeit: Der Prozess ist vielseitig, und kann verschiedenste Metalle inklusive Aluminium, Zink und Magnesium verarbeiten.
- Hohe Produktionsraten: Der Prozess ist relativ schnell, was sehr hilfreich sein kann, wenn unter Zeitdruck produziert wird
- Kosteneffizient: Der Vorgang an sich ist relativ günstig, wodurch er eine kosteneffiziente Option für viele Anwendungen darstellt
- Wiederholbarkeit: Der Prozess erlaubt außerdem, dass viele Teile wiederholt und dennoch mit ganz genauen Spezifikationen produziert werden können.
Anwendungsgebiete des Druckgusses
Der Druckguss wird in verschiedenen Industrien und Anwendungsgebieten verwendet. Einige der am häufigsten Anwendungen für den Druckguss sind:
- Automobilindustrie: Der Druckguss wird extensiv in der Automobilindustrie verwendet. Man verwendet ihn dort zum Beispiel oft für Motorblöcke, Zylinderköpfe oder Getriebekästen.
- Elektroindustrie: Die Elektroindustrie verlässt sich ebenfalls bei vielen Anwendungen auf den Druckguss. Druckgussteile werden bei der Herstellung von Schaltanlagen, Schalttafeln und Leistungsschutzschaltern verwendet.
- Luftfahrtindustrie: Die Luftfahrtindustrie ist einer der häufigsten Anwender des Druckgusses. Die gefertigten (leichten und dennoch stabilen) Teile werden beim Bau von Flugzeugen und Raketenteilen verwendet.
- Möbelindustrie: Der Druckguss wird auch oft in der Möbelindustrie verwendet, um dort zum Beispiel Griffe und Knäufe herzustellen.
Viele andere Industrien nutzen den Druckguss ebenfalls, zum Beispiel in der Medizin, dem Bauwesen oder der Spielzeugindustrie. Er ist ein vielseitiger Prozess, der ganz unterschiedliche Teile oder ganze Produkte hervorbringen kann.
Mit dem Druckguss anfangen
Der Druckguss ist ein Fertigungsverfahren, dass schon für Jahrhunderte Bestand hat, und immer noch populär ist, weil es so vielseitig ist und die Fähigkeit hat komplexe Formen zu erschaffen. Das Verfahren kann Metallteile für eine Vielzahl von Industrien erschaffen, zu denen die Automobil-, die Luft- und Raumfahrt-, die Möbel- und Haushaltsgeräteindustrie gehören.
Durch unser weitreichendes Netzwerk an Herstellern bietet Ihnen Xometry Europe Druckgussleistungen für mehrere Dutzend Materialien inklusive Aluminium, Magnesium und Zink an. Schauen Sie einfach rüber zu unserer Instant Quoting Engine und laden Sie ihr Modell hoch, um direkt ein Angebot zu erhalten und die Teile bestellen zu können.
Comment(0)