Bei FBRC interessieren wir uns besonders für Redox-Flow-Batterien, da sie kostengünstige, sichere und nachhaltige Lösungen zur Speicherung erneuerbarer Energien bieten. Ihr relativ einfacher Aufbau und die wasserbasierten Elektrolyte machen es möglich, kostengünstig zu forschen und zu entwickeln – ganz im Gegensatz zu Lithium-Ionen-Batterien, für deren Entwicklung und Produktion weitaus teurere Einrichtungen erforderlich sind.
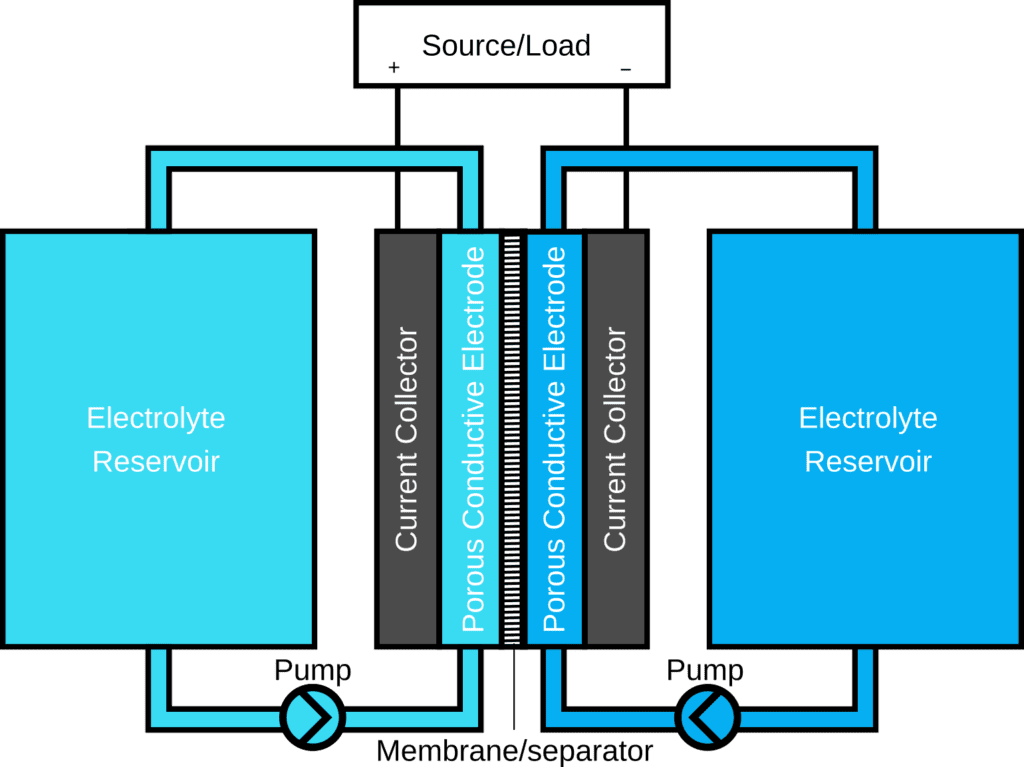
Durch die Öffnung dieser Technologie und unseren Open-Source-Ansatz wollen wir die Innovation im Bereich der Redox-Flow-Batterien beschleunigen. Langfristig planen wir, Designs und erste Prototypen einer funktionierenden Redox-Flow-Batterie unter einer Open-Source-Lizenz zu veröffentlichen, die auch kommerzielle Nutzung erlaubt.
Um dieses Ziel zu erreichen, müssen wir die spezifischen Eigenschaften dieser Batterien im kleinen Maßstab präzise testen. Aus diesem Grund haben wir ein Entwicklungskit erstellt, das sowohl reproduzierbare Forschungstests als auch den Einsatz in der Lehre ermöglicht.
Von Hackerspaces zu hochpräzisen Bauteilen: Entwicklung einer Open-Source-Redox-Flow-Batterie
Unser Team fand über das Internet zusammen – wir stießen auf die Blogs der anderen und stellten schnell fest, dass wir alle in verschiedenen Ländern der EU leben. Unser Entwicklungsprozess verlief daher geografisch verteilt: Ich entwarf die Teile in Frankreich, Josh fertigte sie in Lilis Proto-Labor in den Niederlanden an und schickte sie dann an Daniel in Spanien zur experimentellen Prüfung. Für erste Prototypen mittels FDM-Druck funktionierte dieses Vorgehen gut.
Unser Ziel war es, ein erschwingliches Redox-Flow-Batterie-Entwicklungskit zu schaffen, das leicht herzustellen ist und dessen Komponenten problemlos zu beschaffen sind. Ein wichtiger Fortschritt war die Entwicklung einer Zelle, die kostengünstiges und gut verfügbares Graphitfolien-Dichtungsmaterial als Stromabnehmer nutzt, anstelle des teureren und schwer erhältlichen Bipolarplattenmaterials. Neben der Durchflusszelle und dem Elektrolyten wollten wir das gesamte System open-source gestalten – von Pumpen und Schläuchen über Reservoirs und Vorrichtungen bis hin zur Leistungselektronik. Uns war es wichtig, ein vollständiges System bereitzustellen, um die Einstiegshürden so niedrig wie möglich zu halten.
Die erste Version unserer Zelle erforderte bearbeitete Polypropylen-Teile. Beim Versuch, diese Teile mit FDM-Druck herzustellen, stießen wir jedoch auf Probleme: Resin-Drucke erwiesen sich als chemisch nicht kompatibel mit unseren Elektrolyten.
Innovationen skalieren: Wie die digitale Fertigung Open-Source-Energiespeicherung ermöglicht
Prof. Sanli Faez bot uns an, unser Projekt im Rahmen seines FAIR Battery-Projekts bei einem Workshop in den Niederlanden vorzustellen. Bei diesem Workshop sollten die Teilnehmer gemeinsam Zellen (mit Wasser) zusammenbauen. Um dieses Ziel zu erreichen, benötigten wir in kurzer Zeit 20 bearbeitete Zellkörper, um 10 vollständige Kits bereitstellen zu können.
Hier kam Xometry ins Spiel. Wir sind in erster Linie Forscher und keine Fertigungsexperten. Für bestimmte Anwendungen gibt es keinen Ersatz für gefräste Teile, weshalb wir uns an Xometry wandten, um diese Komponenten für unseren Workshop herzustellen. Mit den geladenen Elektrolyten, die wir für Tests verwendeten, darunter Triiodid-Spezies, die mit anderen FDM-Materialien wie ABS reagieren, die sonst in sauren Elektrolyten stabil sein könnten. Daher entschieden wir uns, diese aus massivem Polypropylen zu fräsen, sobald wir wussten, dass die Geometrie und der Ansatz unserer Zelle funktional waren. Nachdem wir die Funktionalität unserer Zellgeometrie bestätigt hatten, nahmen wir nur eine kleine Anpassung vor: Wir fügten Gewindebohrungen hinzu, um handelsübliche Schlauchtüllen zu befestigen, da diese Geometrie nicht fräsbar war.
Dank Xometry erhielten wir die benötigten Teile rechtzeitig für den Workshop. Die Montage verlief reibungslos, und der Workshop war ein voller Erfolg.
Seit dem Workshop haben wir Fortschritte in Richtung einer verbesserten Version des Kits gemacht, die den Herstellungsprozess vereinfacht. Wir benötigen keine bearbeiteten Kunststoffteile mehr, aber es gibt einige Metallkomponenten, die weiterhin am besten durch subtraktive Bearbeitung hergestellt werden.
Als Open-Source-Hardwareentwickler sind wir neidisch auf die Leichtigkeit, mit der Softwareentwickler ein Repository klonen und Beiträge leisten können. Ingenieure, die Leiterplatten entwickeln, verfügen nun auch über standardisierte Open-Source-Tools wie KiCAD und eine Vielzahl von Herstellern, die schnelle Durchlaufzeiten bieten, was die Entwicklung erleichtert und die Iterationszyklen für PCB-basierte Projekte verkürzt.
Mit digitalen Fertigungsdiensten und Open-Source-CAD-Tools wie FreeCAD wird es einfacher denn je sein, kundenspezifische Teile von einer globalen Community entwickeln und testen zu lassen. Wenn 3D-Druck nicht ausreicht, können Projekte wie unseres aufgrund des Engpasses beim physischen Zugang zu einer Werkstatt mit konventionellen Werkzeugen und erfahrenen Mechanikern ins Stocken geraten oder zum Stillstand kommen. Ohne diese Einschränkung können Projekte wie unseres innovieren, iterieren und es anderen ermöglichen, unsere Arbeit viel einfacher nachzuvollziehen und dazu beizutragen als zuvor.
Sie können den Fortschritt unseres Projekts hier verfolgen und in unser Forum einsteigen, wenn Sie Fragen haben
Wie haben digitale Fertigungstechnologien eure Entwicklung beschleunigt? Welche Erfahrungen habt ihr mit Open-Source-Hardwareprojekten gemacht? Wir freuen uns auf eure Einblicke!
**@****al.coop„>Teilen Sie Ihre Konstruktions- oder Produktdesign- Story
Teilen Sie Ihre Story!
Lassen Sie uns an Ihrem Weg der Entwicklung und des Produktdesigns teilhaben und erhalten Sie eine Prämie von 300 €! Zeigen Sie unserer Community Ihre innovativen Lösungen und bewährten Verfahren.
Comment(0)